Fire door products factory conditions inspection points
This Might Be the Most Comprehensive and Detailed Checklist for Fire Door Factory Inspections in All of China—One Sheet Is All You Need for Procuring Fire Doors. Guangdun Door Industry Co., Ltd. has dedicated its entire life, drawing on 20 years of experience, to helping engineers procure fire doors.
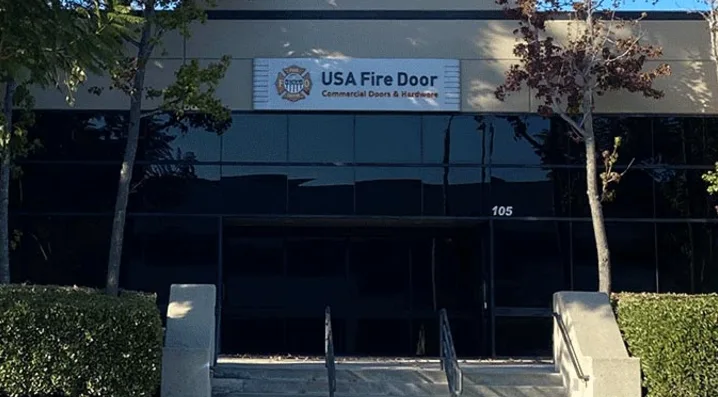
Terms | Terms content | rank | Prepare information | person liable | target date |
1 | Laws, regulations and related policies | ||||
1.1 | Before the first meeting, the enterprise should be required to provide the original fire door product type approval certificate, and compare the status information of the fire protection product information and the information of the production and operation status of the enterprise. | Product sales flow direction information upload table | |||
1.2 | Check the original copy of the business license of the enterprise to see whether it has the manufacturing qualification of fire door products. | * | Original copy of the business license | ||
1.3 | The manufacturer of fire door products shall formulate and implement the safety production system according to the relevant national laws and regulations. The dangerous parts of the production facilities and equipment of the enterprise shall have safety protection equipment, and the workshop and warehouse places shall be equipped with fire fighting equipment, and shall meet the relevant requirements of the building fire prevention code. Flammable and explosive dangerous goods shall be isolated and protected according to the regulations | * | 1. Preparation of the Safety Production System2. Adding the Safety Regulations for Equipment Operation shall include the operation of elevator, driving, welding and manual hydraulic forklift.3. Regulations on the storage environment of fireproof glue4. The punch machine shall be equipped with an infrared protective device5. The reliability test device shall be isolated with a safety net6. Configuration of fire-fighting equipment7. Electric welder, sawing workers with protective cover8 According to the system requirements and can be verified | ||
1.4 | The enterprise shall provide production safety and labor protection training, and provide necessary labor protection measures. | * | 1. Prepare training materials for safety and labor protection2. Organize the training for employees and keep records3. Labor prevention supplies in each workshop have been issued and used, and can be verified. | ||
2 | Production capacity, scale, and conditions | ||||
2.1 | Check the original and original copy of the business license of the enterprise, and record the amount of its registered capital | prepare | |||
2.2 | Check the ownership of the plant to see whether it is a plant; check the lease term and record it | “Plant Lease Contract” | |||
2.3 | Check whether the enterprise sets up departments covering product design and development, production, process, quality inspection, storage, after-sales service and other important responsibilities | * | Whether the organization chart is reasonable | ||
2.4 | Check the number of employees with senior and intermediate technical titles, and record them. | Archives (declaration: senior 5, intermediate 25, junior 10, the total number of fire doors 250) | |||
2.5 | 1. Check whether the cutting, punching, folding technology and equipment capacity of steel door fans and door frames on the processing site are reasonable; whether the processing capacity matches the output declared by the enterprise; whether the equipment accuracy can continuously meet the processing accuracy requirements of the process documents related to mass production; whether the energy saving and consumption reduction measures such as combined processing are adopted.2. Check whether the enterprise has identified and effectively controlled the key process (fire proof material filling and forming process).3. Check the types of inner filling materials used by the enterprise to see whether they are within the scope of being eliminated; see whether they can provide evidence to meet the requirements of combustion performance A1 level stipulated by GB8624-2006 and ZA 2 level stipulated by GB / T20285-2006.4. Check whether the adhesive used by the enterprise can provide evidence that the national authorized testing institution meets the requirements of ZA 2 stipulated in GB / T20285-2006.5. Check whether the other materials used by the enterprise can provide the evidence of ZA 2 required by the authorized testing institutions; whether the evidence shall meet the requirements of GB / T8625-2005 or GB8624-2006; whether the mechanical properties meet the relevant standards and meet the relevant requirements of fire doors.6. Check whether the fire lock, fire hinge, fire closed door device, fire seal, fire glass and other accessories used by the enterprise have passed the inspection by the state recognized and authorized testing institutions.7. Check whether the enterprise has the phosphorization treatment equipment required for steel treatment, whether the process is advanced and environmental protection, and check whether the “three wastes” treatment and device have passed the audit of the relevant national environmental protection department.8. Check whether the painting process of the enterprise has passed the audit of the relevant national environmental protection department. | * * | 1. Production equipment ledger(Applied output: 30,000 square meters / year)Description of the energy-saving and consumption-reduction test2. Prepare the key process control procedures. Each workshop director checks the operation instructions according to the standard, assemble the bonding process points out the bonding process (temperature, time, method), and identify and control the key process of the instruction.Comprehensive evaluation of the filling materialsProvide the test report issued by the national authorities5. Test the mechanical properties of fire adhesive and prepare test operation procedures6. National authority test report of all hardware, glass, fire and smoke proof bars (keep up to date, fire rating of 90 minutes)7. “Three wastes” test report8. Environmental assessment of the painting workshop | ||
2.6 | Check whether the enterprise has external processing or purchased parts that play a key role in the quality of fire door products; if so, whether the enterprise has the drawings, standards, process requirements and acceptance documents that meet the requirements, and the inspection equipment and inspection personnel that meet the requirements. | * | No external processing | ||
2.7 | Check whether the enterprise has a certain medium-term and long-term development strategic plan and annual work objectives, and make regular assessment. | Formulate medium-and long-term development plansThe 2009 policy objectivesPrepare the monthly assessment system and detailed rulesRegular assessment of the completion of targets | |||
3 | Design and development capabilities | ||||
3.1 | Check whether the enterprise has established an organization specializing in product design and development. | * | Organization chart, and at the same time to improve 7.3 products according to the system requirements | ||
3.2 | Check whether the enterprise is equipped with various professionals suitable for product design and development. | * | Designer qualification list | ||
3.3 | Check the amount of r & d investment of the last year, the total amount of fire door sales of the last year, and record it. Calculate the ratio of R & D investment to sales volume. And record. | Provided as required | |||
3.4 | Check whether the enterprise establishes technical files for the technical personnel engaged in product development, including education, work experience and training records, design and development results, etc. | * | Establish technical personnel files | ||
3.5 | Check the enterprise is to establish their own product development document work procedures, and can be applied in practical work. | * | Product design and development control procedures are included in the systemExpand it and enrich the content according to the program | ||
3.6 | Check whether the enterprise has established a product information database with reference value corresponding to the product. | Online information about fire door products, establish a database (based to electronic file) | |||
3.7 | Check whether the enterprise has formulated the design operation instruction used to guide the specific design work of the design personnel. | Design the work instruction book | |||
3.8 | Check whether the enterprise has carried out the advance planning of fire door product development or standard version replacement, and keep the relevant planning records. Plan output whether the “new product development book”, “new product development overall quality plan” or similar documents. | Product development documentsOverall quality plan for new product developmentThe design and development documents should have a general description of the replacement version | |||
3.9 | Check whether the input content of enterprise product design and development is clear and complete; whether it includes customer requirements for products, market information, previous development experience, product function and performance requirements, mandatory technical regulations of national or industry standards, relevant laws and regulations, and characteristic requirements for product safety and applicability. Whether the input of the design and development forms the corresponding documentation. | Enrich according to the system requirements | |||
3.10 | Check whether the enterprise product design and development output has formed a document, and whether it includes the following contents:product drawing;Product process documents;Summary table of purchased parts;Classification of key parts, important parts features or similar documents;Summary table of standard parts;Inspection and operation instructions for key parts and important parts;Product enterprise standards;Product assembly technical conditions, product factory inspection specifications;Product use instructions;Design calculation book. | Article tents 1-10, | |||
3.11 | Check whether the enterprise has made the following process documents for its own key parts:Process procedure documents;List of tooling and inspection tools;Inspection operation instruction book; | ||||
3.12 | Check whether the enterprise has formulated the enterprise standards of fire door products (including the performance and quality standards of the internal filling materials, the formaldehyde release limit standards of fire boards and adhesives, etc.), whether the requirements are higher than the corresponding national or industry standards, and handle the formalities according to the provisions. | * | Product enterprise standard preparationStandard record | ||
3.13 | Check the enterprise is for the product design and development review, and keep the corresponding records. | Design and development review and record | |||
3.14 | Check whether the enterprise has designed and developed the products, and whether the samples have been verified (including test verification) to confirm that they meet the specified requirements. | Sample test dataSend sample detection | |||
3.15 | Check whether the enterprise has implemented stage confirmation or batch production confirmation for the design and development and products, and confirm including all the mandatory inspection items involved and the relevant items stipulated in the national standards and industry standards. | Be full as required | |||
3.16 | Check whether the enterprise verifies the production process and equipment (including process documents, personnel, production equipment, inspection equipment, environment, etc.). | * | Equipment maintenance, major and medium repair plan, recordAssessment record of production environment control (refer to Q / ZXFC019-2006 Control of Production Environment)The verification period of all inspection equipment has arrived and shall be sent for external inspectionDesign and fill in the Production Process and Equipment Verification Form | ||
3.17 | Important design changes affecting safety and environmental performance shall be reviewed, verified and confirmed according to the product design and development process control procedures, and shall be adopted only after the sample trial production meets the requirements. Design change review and confirmation records shall be kept. | * | This requirement is reflected in the system document | ||
4 | After-sales service ability | ||||
4.1 | Check whether the enterprise has established a full-time after-sales service organization, with enough training and good after-sales service personnel, sufficient zero, accessories and rapid response mechanism, and implement it. | * | After-sales service is assigned to the comprehensive service department, which is reflected in the responsibilities of the departmentAfter-sales service personnel trainingSufficient parts and accessories (to clarify the minimum inventory) and rapid response mechanism, and to be implemented in Q / ZXFC024 “Service Management Standards”, and be verified, to have training records and verification records | ||
4.2 | Check whether the enterprise has established a perfect customer file. | * | Establish block case (customer files involved in fire tag uploading) | ||
4.3 | Check whether the enterprise has sufficient training ability, and should meet the training requirements for distributors / agents and users. | Make the PPt training materialsMaterial providedPPt fabrication | |||
4.4 | Check whether the enterprise has established a quality information feedback mechanism. | Check whether the Quality Responsibility Assessment Management System and the Service Management Standard in the system conform to this clause | |||
4.5 | Check whether the enterprise has established effective site installation and construction specifications of fire door products, and implement them carefully according to the regulations. | * | Check the contents of “Internal Control Standard for Fire Door Installation”, “Installation Operation Instructions” and “Installation Inspection Record”, and enrich them according to the contents | ||
5 | 产品一致性 | ||||
5.1 | The enterprise shall establish a documented quality management system according to the 15 basic conditions of the factory or the GB / T19001 standard; check whether the enterprise has obtained the GB / T19001 quality management system certification certificate issued by the certification body. | * | System certification certificateThe system is improved according to the standards, and it is implemented | ||
5.2 | Check whether the enterprise is responsible by qualified professionals for standardization and has reliable channels to timely obtain national standards and industry standards related to products. | ||||
5.3 | Check whether the enterprise has reviewed the impact of existing products for the version change of fire door product standards, and taken corresponding measures to keep relevant records. | * | Prepare review report | ||
5.4 | Check whether the enterprise transforms the mandatory standards and industry standards related to the product into operational information, which is reflected in the product documents (enterprise standards and product drawings, etc.), process operation documents (process documents and operation instructions, etc.). | * | References of the enterprise standards to the system file | ||
5.5 | Check whether the product drawings and related technical documents are complete, and whether they are effectively used to guide the production. | * | self-inspection | ||
5.6 | Check whether the main inspection equipment involved in the production of the enterprise has been calibrated or verified according to the specified period. | * | External inspection is required | ||
5.7 | Check whether the performance indicators of the enterprise inspection equipment meet the requirements of the rules and technical standards and are consistent with the required measurement capacity. | * | Self-check the Operation Instructions, indicating the accuracy of the inspection instrument | ||
5.8 | 1. Check whether the inspectors of the enterprise have been trained, assessed and have corresponding qualifications, and carry out actual operation according to the inspection operation instructions.2. The inspection team shall select the completed certified products (one product for each product category). The finished product inspection personnel confirmed by the factory shall, under the supervision of the requirements of the inspection team, inspect the existing inspection equipment of the factory and issue the relevant inspection records, which shall be sealed and signed by both the inspection team and the inspection company. | * | Inspector trainingArrange the inspector | ||
5.9 | Check whether the enterprise has carried out process monitoring and measurement of key processes and special processes, and prepared work instructions, whether these instructions can be easily available in the work site. | * | Key processes and special processes shall be executed according to the newly prepared Key Process Control ProcedurePreparation of instructionsProduction of the instruction bookPaste the instruction book on the spot | ||
5.10 | 1. Check whether the enterprise has established clear acceptance requirements for the key parts involved in safety and environmental protection performance, including quantity, quality confirmation, sampling inspection and other links. Batch procurement can be carried out only after determining that the technical conditions of the relevant products are met, and the corresponding records shall be kept. Whether the enterprise has concessions to accept the safety, the environmental performance does not meet the requirements of the key components.2. In the selection of internal filling materials, enterprises must specify the following parameters and indicators:1) Density (kg/m3);2) Thermal conductivity (w / cmK);3) Compressive strength (MPa);4) Resistance strength (MPa);5) Quality and moisture content (%);6) Moisture absorption;7) Contraction rate;8) Fire protection performance requirements;3. In the selection of fire proof board and adhesive, etc., enterprises must clarify the requirements of formaldehyde release limit | * | Re-compile the Procurement Documents and the Inspection Procedures for Raw and Auxiliary Materials and keep the inspection recordsExcept for the technical indicators to be inspected by the factory, the other technical indicators are guaranteed to be provided by the supplier, and provide the test report issued by the national authority | ||
5.11 | Check whether the enterprise has clear acceptance requirements for general parts and outsourcing parts, including quantity, quality confirmation, sampling inspection and other links. Whether the batch purchase can be carried out only after meeting the relevant product technical conditions, and the corresponding records are kept. | Check the procurement documents and inspection records | |||
5.12 | Check whether the enterprise evaluates and selects the supplier in an appropriate way, whether the evaluation content of the raw material supplier related to the safety and environmental protection regulations includes the product physical quality, quality system operation status, manufacturing capacity, technical ability, inspection ability and quality improvement status, etc., and keep the corresponding records. Whether the specifications, models and performance parameters of raw materials and outsourcing parts related to safety and environmental protection performance are consistent with the product design documents, and shall be purchased from the qualified supplier. | Comprehensive evaluation of suppliersList of qualified suppliers | |||
5.13 | If the products provided by the supplier or the supplier are changed and affect the contents of the original agreement, the enterprise shall take appropriate corrective and preventive measures to implement and verify their effect. | Preparation of purchase agreement (handling method when applied product changes) | |||
5.15 | Check whether the enterprise regularly conducts self-examination of the status of meeting the type recognition, and make a good record. | * | Compile and implement self-inspection regulations of fire prevention products | ||
6 | Certificates and flags and usage | ||||
6.1 | Check whether the enterprise has established the management regulations on the storage and use of the certificate, and whether it meets the requirements. | Follow the Document Control Procedure, and it can be verified | |||
6.2 | Check whether the enterprise has established the management system of identity information marks of fire products, whether it covers the purchase, storage and use of standard products; whether it is marks on the factory products according to the regulations; | * | Consult the “fire door product access mark management rules” and improve | ||
6.3 | Check whether the enterprise has established the management system of special goods in the fire product tracking management system, whether it covers the storage and use of special goods; and whether the identity information mark of fire products is added on the factory products according to the regulations; | * | |||
6.4 | Check whether the enterprise has uploaded the sales flow information of fire door products in accordance with the rules. Whether the uploaded information in the database is consistent with the enterprise production and sales records. | * | Fire door production records and sales records shall be consistent with the uploaded logo. |
If the identification is “*” in the level, it is a veto clause. If any one does not meet, the factory condition inspection conclusion is not recommended.
В тумане или в темноте тепловизор незаменим как для охотников, так и для военных.
Review my web page: тепловизоры
Тепловизор идеально подходит для охоты на диких животных в темное время суток.
Here is my web site купить тепловизор для военных (https://utahsyardsale.com/author/harry635941/)
Hi mates, how is everything, and what you want to say regarding this piece of writing, in my view
its genuinely awesome in favor of me.
Hello, yeah this piece of writing is genuinely good and I have learned lot of things from it about blogging.
thanks.
Hi there to every body, it’s my first pay a visit
of this web site; this web site includes amazing and truly excellent information designed for visitors.