Steel fireproof door compliance with GB 12955-2008 standards Development of hot-dip galvanized steel plate production and galvanizing technology in China, as well as the application of fireproof door manufacturing Steel fireproof door compliance with GB 12955-2008 standards
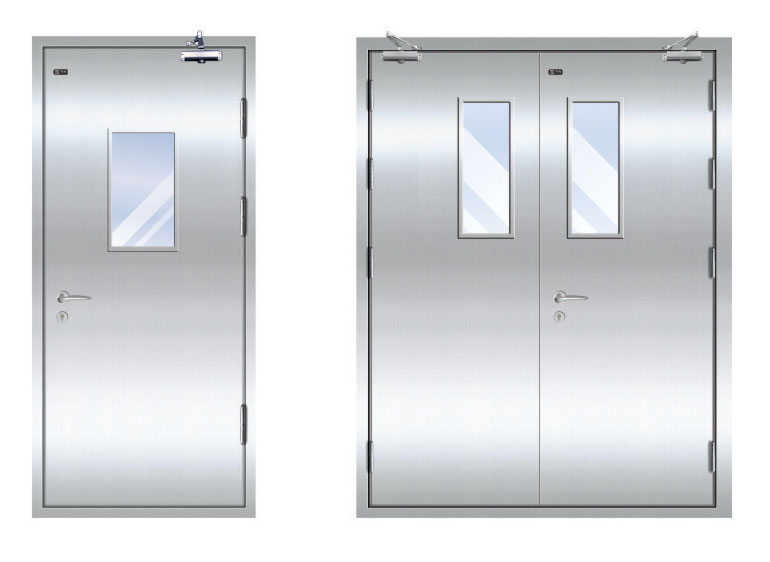
Due to its excellent corrosion resistance, appealing appearance, suitability for subsequent processing, cost reduction, and minimal environmental impact, hot-dip galvanized steel sheet is highly favored by a wide range of users.
Overview of Hot-Dip Galvanized Steel Sheet Production in China
During the 1950s to 1970s, China successively constructed about 15 sets of individual solvent-based hot-dip galvanizing units, with a total capacity of approximately 100,000 tons per annum (t/a). This process utilized hot-rolled pickled plates as raw materials. However, due to poor product quality, high costs, and environmental pollution, these units were phased out in the 1980s. In 1979, Wuhan Iron and Steel Corporation imported and established China’s first continuous hot-dip galvanizing unit from Germany, with a capacity of 150,000 t/a. By the 1990s, the production of continuous galvanized steel in China experienced rapid development, with 11 continuous hot-dip galvanizing units nationwide, reaching a total capacity of 1.82 million t/a, accounting for approximately 2% of the total steel output.
In the early 21st century, alongside the rapid development of the national economy and the structural adjustment of the steel industry with an increased proportion of flat materials, the construction of galvanizing units surged. Major state-owned steel enterprises such as Pangang, Baosteel, Ansteel, Wugang, Magang, Benxi Steel, Handan Steel, and Tangsteel all established hot-dip galvanizing units. These large state-owned enterprises, with their strong economic and technical capabilities, constructed galvanizing units with technology imported from abroad, high equipment levels, and high production capacities (generally 350,000 to 500,000 t/a), targeting high-end products. The main markets for these products include the automotive, home appliance, and high-quality building materials sectors. Some of these units were joint ventures between state-owned enterprises and foreign companies, such as Baosteel’s 450,000 t/a galvanizing unit built in partnership with Nippon Steel and Arcelor, Ansteel’s 400,000 t/a unit in Dalian Development Area with ThyssenKrupp, and Guangsteel’s 400,000 t/a unit in Guangdong Nansha with JFE, primarily focusing on car panels.
During this period, private enterprises also invested in constructing galvanizing units, with steel traders as the backbone of investors, focusing on building standalone galvanizing units. These enterprises, familiar with raw material procurement and possessing a vast network of downstream customers, demonstrated significant market and operational expertise. Some financially stronger private entrepreneurs started from complete cold rolling mills, with their galvanizing units mostly using domestic technology and equipment, and a few importing minor parts and key standalone equipment. These units, with capacities mostly below 200,000 t/a, and many around 100,000 to 150,000 t/a, mainly targeted the general building materials market. Despite lower overall investment and production costs, they remained highly competitive.
By the end of 2005, China’s large state-owned steel enterprises (including joint ventures) had built over 40 high-capacity hot-dip galvanizing units, with a total capacity exceeding 15 million t/a; private enterprises had constructed more than 80 galvanizing units, with a total capacity nearing 15 million t/a. In terms of capacity, state-owned and private enterprises each accounted for half of the market. However, when considering product grade, quality, raw material and energy supply, and technical strength, the large state-owned steel enterprises still held a competitive edge.
According to statistics from the China Iron and Steel Industry Association, from 1999 to 2004, China’s galvanized sheet output was 1.45, 1.67, 2.2, 2.6, and 4.17 million tons, growing at an average annual rate of 23.5% (excluding galvanized sheets produced by private enterprises). From 1999 to 2003, the import volume of galvanized sheets increased at an average annual rate of 37.3%, but in 2004, it dropped to 4.35 million tons, a decrease of 1.02 million tons from 2003, marking an unprecedented decline. From 1999 to 2003, China’s galvanized sheet export volume was generally below 100,000 t/a, with an average annual export volume of 81,200 tons. However, in 2004, the export volume of galvanized sheets surged to 522,000 tons, 6.4 times the average of the previous five years. In the first quarter of 2005, compared to the same period in 2004, the production of galvanized sheets increased by approximately 40%, while imports sharply decreased by 31%, and exports grew by 11.8%.
From the data above, it is evident that by 2004, China’s steel structure adjustment had begun to show results, with the self-sufficiency rate of deep-processed galvanized sheet materials increasing, and China’s production of hot-dip galvanized sheets starting to enter the international market.、
Trends in Hot-Dip Galvanized Steel Sheet Production Technology
The development trends in the production technology of hot-dip galvanized steel sheets are as follows:
(1) Trend towards Higher Production Capacity
Since the 1990s, newly constructed hot-dip galvanizing units have trended towards higher production capacities. Globally, there are approximately 60 sets of hot-dip galvanizing units with capacities exceeding 300,000 tons per annum (t/a), totaling a production capacity of over 28 million t/a.
(2) Specialization of Units
Different types of units are utilized for producing automotive galvanized sheets and building material galvanized sheets. The process, individual equipment configuration, and furnace selection are more rational, resulting in significant investment benefits and reduced product costs.
(3) Emphasis on Substrate Surface Cleanliness
Recently built automotive sheet galvanizing units primarily adopt the American Steel Union process, which uses alkaline electrolytic cleaning and full-radiant tube heating furnaces, even placing cleaning sections before and after the looper devices. To reduce investment, building material galvanizing units often use the improved Sendzimir process, but still incorporate cleaning sections to ensure cleaner substrate surfaces and better product quality.
(4) Adoption of Tower Furnaces
Using a tower furnace, which costs approximately 25% to 30% more than a horizontal furnace, was historically justified for units with capacities over 300,000 t/a due to length limitations of the furnace. After the 1990s, manufacturers have focused more on the advantages of tower furnaces: better gas tightness, fewer and longer-lasting furnace rolls, lower maintenance costs, improved plate shape, and shorter furnace length. Many galvanizing units with capacities of 250,000 t/a or less have also chosen tower furnaces, such as the 250,000 t/a hot-dip galvanizing unit built by France’s Solac in December 1990; the Luxembourg Dudelange steel plant’s 250,000 t/a unit in September 1991; and BHP’s aluminum-zinc unit in California, USA. China has also adopted tower furnaces in several newly commissioned hot-dip galvanizing units.
(5) Continuous Improvement in Furnace Efficiency
Efficiency improvements include using exhaust gas to preheat the steel strip to save energy and prevent strip deformation; continuous furnaces are equipped with cooling sections of various designs based on product requirements; tension leveling rollers are used to optimize in-furnace strip tension; the heating section includes high-precision anti-heat warpage rollers and induction heaters; drum-extraction pulse control burners, multi-stage combustion radiant tubes, and other heating technologies improve burner adjustment range and radiant tube lifespan, ensuring uniform heating, reducing NOx content, and benefiting environmental protection; improvements in furnace roll design and surface coating technology are also implemented.
(6) Continuous Improvement in Galvanizing Equipment
Galvanizing equipment improvements include air knives, sink rolls, stabilizing rolls, and auxiliary equipment, zinc pots, and zinc-feeding equipment. Over the years, air knife manufacturers such as Fonderie, AGC, Duma, and Kohler have focused on innovations, including automatic tracking of the steel strip, maintaining a stable distance from the strip, integrating assembly adjustments with precise positioning mechanisms, achieving dynamic control of nozzle area pressure, using double-lip rotary air knives with optimal gap curves, and incorporating quick cleaning devices for knife lips, significantly enhancing air knife performance. Sink roll designs, zinc trough shapes, spacings, and bearings have also been improved for increased stability and lifespan. Zinc pots often use ceramic-lined channel designs with larger volumes for more stable zinc liquid. For modern large-scale units, the bottom edge of the sink roll is at least 800mm above the pot floor, and even larger for units producing automotive sheets. The development of coreless zinc pots is mature, and SMS has developed a coreless pot using electromagnetic fields to create a magnetohydrodynamic seal in a vertical design, allowing the steel strip to pass vertically through the zinc liquid without any corrosion-prone components inside the pot. This technology has completed industrial trials and received orders from East Steel in Korea, attracting industry attention.
(7) Improved Leveling Performance
Four-roll levelers are used, offering dry and wet leveling processes, large and small diameter working rolls, and roll surfaces treated with shot blasting or electron beam texturing to meet different requirements for elongation and surface smoothness. Different combinations of levelers and tension levelers are used for various product types to achieve optimal results.
(8) Advanced Post-treatment Processes
Depending on user requirements, treatments such as passivation, phosphating, alloying, or applying organic coatings are available. Continuous development and research are being conducted to improve passivating agent formulas. Currently, passivation mainly uses chromates, but with added activators like fluorides and phosphoric acid, thicker chromate films can be obtained; fluoride accelerates the formation of the passivation film, enhancing its fineness and brightness. Research on non-toxic or low-toxicity inorganic corrosion inhibitors as passivating agents has led to the development of a passivating solution (ACM) containing small amounts of molybdate and phosphate in a non-toxic water-soluble acrylic resin, replacing toxic chromates and delaying the onset of white rust, with corrosion resistance approaching that of chromate passivation. Although this technology is not yet fully mature, the trend towards chromium-free passivation to replace chromate passivation is driven by environmental considerations.
Hot-dip galvanized steel sheets treated with phosphating can replace traditional electro-galvanized steel sheets for use in home appliance exteriors, extending product life and reducing material costs. Online phosphating treatment for hot-dip galvanizing units shows great potential. Research hotspots include fingerprint-resistant treatment and the application of inorganic and organic lubricating films.
(9) Development of Zinc Alloy Coatings
Zinc alloy-coated steel sheets offer superior performance compared to galvanized steel sheets, and their production share is increasing annually. Rapidly developing varieties include aluminum-zinc alloy (Galvalume), zinc-aluminum alloy (Galfan), and zinc-iron alloy (Galvanneal) coatings. Nisshin Steel recently developed a zinc-aluminum-magnesium alloy coating (ZAM) with corrosion resistance ten times that of traditional galvanized sheets.
Aluminum-zinc and zinc-aluminum alloy-coated steel sheets have better corrosion resistance, paintability, and formability than standard hot-dip galvanized sheets, making them suitable for the building materials and light industry sectors. Zinc-iron alloy-coated steel sheets offer better paintability, post-paint corrosion resistance, and weldability than zinc-aluminum or aluminum-zinc alloy-coated sheets, and are extensively used in the automotive manufacturing industry.
To accommodate the production of zinc alloy-coated steel sheets, galvanizing units increasingly employ elevating and movable dual galvanizing pots, facilitating quick changes in coating types. In 1998, the American company Applied Materials launched a coreless zinc pot that is energy-efficient and cost-effective, making it highly suitable for alloy coating production. Zinc-iron alloy diffusion furnaces are trending towards using high-frequency induction heating for the heating section and resistance heating for the soaking section, allowing for optimized annealing curves and more precise control over the iron content in the galvanized layer.
(10) Development of Spangle-Free Steel Sheets
Lead-free galvanizing can produce spangle-free steel sheets, which reduce intergranular corrosion, thereby extending their service life, benefitting the environment, and making them suitable for the automotive industry as well as for use as pre-painted substrate. A few years ago, Europe ceased the production of regular spangled steel sheets, indicating a clear trend towards the production of spangle-free steel sheets.
(11) Development of Ultra-Deep Drawing, High-Strength Galvanized Steel Sheets
For the production of automotive-grade ultra-deep drawing and deep drawing hot-dip galvanized sheets, IF steel is used, and continuous furnaces eliminate the over-aging section, simplifying the furnace structure and production control. Manufacturers are focusing on developing high-strength steel hot-dip galvanized sheets. High-strength steels typically have higher Si and Mn contents, which are detrimental to zinc adhesion. Adjustments in chemical composition, especially the addition of Mo, have enabled the successful production of low-Si dual-phase steel galvanized sheets and dual-phase steel galvanized alloy sheets. TRIP hot-dip galvanized steel sheets produced by replacing Si with Al are comparable to traditional CMnSi-type TRIP steels, but the addition of Al presents some challenges in steelmaking and hot rolling processes, which are being addressed.
(12) Production of Ultra-Thin Coating Sheets
Recent improvements in equipment like air knives have enabled the production of hot-dip galvanized sheets with coatings as thin as 25–30g/m2 on both sides, commonly used in the electrical appliance industry, potentially replacing some electro-galvanized or tin-plated steel sheets.
(13) Decline in Single-Sided Hot-Dip Galvanized Sheets
The process for single-sided hot-dip galvanizing is cumbersome and costly, leading to a preference for single-sided electro-galvanized sheets or double-sided differential thickness hot-dip galvanized sheets.
(14) Emphasis on Developing Hot-Rolled Hot-Dip Galvanized Sheets
With increasing focus on energy-efficient materials and the development of thin slab continuous casting and rolling, more thin-gauge hot-rolled coils are being produced, leading to increased attention and development in hot-rolled hot-dip galvanized sheet production. These Steel fireproof door compliance are primarily used in the construction sector for steel structures, cable trays, ventilation ducts, grain silos, etc. Currently, hot-rolled hot-dip galvanized sheets account for approximately 8%–9% of the global galvanized sheet output, with companies like Handan Steel and Tangshan Steel in China having established hot-rolled hot-dip galvanizing units.
(15) Increasing Level of Automation Control
The entire line is computer-controlled, enabling optimization and closed-loop control of line speed, tension, roll alignment, furnace temperature at various sections, furnace atmosphere, zinc pot temperature, and coating thickness.
Challenges in China’s Galvanized Steel Sheet Production
Currently, China’s galvanized steel sheet production faces the following challenges:
(1) Excess of Low-Capacity Units
In recent years, China has built too many hot-dip galvanizing units with capacities below 200,000 t/a, some with capacities as low as 100,000 t/a or less. These units occupy more land per unit of capacity and face numerous environmental challenges due to dispersed pollution control. Additionally, product yield rates are low, and product quality is not high.
(2) Potential Overcapacity in Galvanizing Units
In recent years, companies like Baosteel, Ansteel, Wugang, Benxi Steel, Magang, and Guangsteel-JFE have constructed or are constructing automotive-grade galvanizing units. Including planned units, the total capacity exceeds 5 million t/a. Assuming 60% of this capacity produces car panels, this equates to 3 million t/a. In 2005, China planned to produce 2.28 million cars, requiring 1.34 million tons of sheet metal, of which only 500,000 tons are galvanized sheets; by 2010, the planned production was 4 million cars, requiring 2.26 million tons of sheet metal, of which only 860,000 tons are galvanized sheets. The construction of so many automotive-grade galvanizing units, if the surplus galvanized sheets for cars cannot be exported and are instead used for building materials, is economically inefficient, as the investment in an automotive-grade galvanizing unit is 3 to 4 times that of a building material galvanizing unit. Moreover, it is difficult for the building material galvanized sheet market to quickly absorb over 20 million t/a, leading to potential overcapacity and unprecedented market competition after 2006 or 2007.
(3) Lack of Building Material Zinc Alloy-Coated SheetsSteel fireproof door compliance.
Recent automotive-grade hot-dip galvanizing units are typically equipped with zinc-iron alloying furnaces, and the production capacity for zinc-iron alloy-coated sheets meets current demands. Companies like Baosteel, Pangang, and Xin Da Zhong have constructed units for aluminum-zinc (Galvalume) or combined aluminum-zinc coating, but the output is limited. Building material zinc-aluminum (Galfan) alloy-coated sheets have excellent performance, with a higher production share abroad, but currently, there is no domestic production.
(4) Reliance on Purchased Substrates
Many of the standalone galvanizing units in China use purchased galvanized base plates, leading to increased packaging and transportation costs, affecting the economic benefits of enterprises.
(5) Uneven Distribution
Although China has constructed over a hundred hot-dip galvanizing units in recent years, they are mainly concentrated in Shanghai, Jiangsu, Hebei, Liaoning, Hubei, Shandong, Zhejiang, Sichuan, Fujian, and other provinces and cities, accounting for over 90% of the total capacity. Other provinces and cities do not have a single wide-strip hot-dip galvanizing unit, resulting in highly uneven distribution.
(6) Thin Coatings on Building Material Hot-Dip Galvanized Sheets
The current market for building material hot-dip galvanized sheets in China is not well-regulated, with many companies having a weak sense of standards. To reduce production costs, they continually reduce the thickness of the galvanized coating. In hot-dip galvanized sheet production, the consumption of zinc ingots accounts for about 60% of the additional costs. When used outdoors, especially, the thickness of the zinc layer determines the service life of the sheet. Typically, the zinc coating thickness for outdoor use should be 275g/m2 (double-sided), with a coating thickness of 20μm, ensuring a 20-year outdoor service life. Currently, state-owned enterprises produce hot-dip galvanized sheets with zinc coating thicknesses of about 150–200g/m2 (double-sided), while private enterprises produce sheets with thicknesses of about 80–100g/m2 (double-sided), significantly reducing the lifespan of outdoor structures and causing immeasurable losses to users.
(7) Low Production of Spangle-Free Steel Sheets
Currently, China’s building material galvanizing units primarily produce regular spangled steel sheets, which are widely accepted in the market, while the production of spangle-free steel sheets is too low. However, regular spangled steel sheets are prone to intergranular corrosion and have inferior corrosion resistance compared to spangle-free sheets, making them less ideal as substrates for pre-painted coils. Additionally, the addition of lead to the zinc ingots results in high lead content in the zinc layer, which is not environmentally friendly, hence the need to promote spangle-free steel sheets.
(8) Incomplete Production Statistics Affect Market Research.Steel fireproof door compliance.
Many market research reports lack data on private enterprises, and incomplete statistics pose significant challenges to market research, sometimes even leading to incorrect conclusions that affect decision-making. China has built several world-class hot-dip galvanizing units and introduced some hot-dip galvanizing production software, capable of producing building material galvanized sheets, home appliance galvanized sheets, and some car galvanized sheets. However, further in-depth research on galvanizing processes is needed, with more efforts in developing and innovating technologies.
Several Hot Issues
(1) Coordinated Development between the Coating Industry and Upstream Resources
Large steel enterprises, when producing coated steel sheets, benefit from a complete production system that allows for timely adjustments in steel grades and dimensions according to orders, resulting in short delivery times. Additionally, due to self-supply of raw materials, these enterprises can save on costs related to packaging and transportation of galvanized base coil; they also have blast furnaces, coke ovens, and converters, enabling the production of by-product gases and oxygen, which provides favorable energy conditions. Furthermore, due to the specialization and number of units constructed, these enterprises can enhance efficiency, stabilize product quality, and thus strengthen their competitiveness.
However, given the overall scarcity of mineral resources in China, large steel enterprises are actively seeking mineral and energy resources. Companies such as Baosteel, Wugang, Shougang, Magang, and Tangsteel have formed joint ventures with Brazil and Australia for iron ore mining and have invested in domestic coal mines to maintain long-term competitiveness.
Enterprises focused solely on producing hot-dip galvanized sheets often lack these advantages. However, these enterprises typically rely on domestic equipment, which requires less investment and depreciation, has lower operating costs, lightens the corporate burden, and offers flexible management, providing a competitive edge. These enterprises should establish stable substrate supply channels and long-term cooperative relationships.
(2) Minor Impact of Ore and Energy Price Increases on Coated Steel Sheets,Steel fireproof door compliance.
Since 2004, the continuous rise in ore and energy prices has directly impacted the cost of steel products. However, the cost impact on hot-dip galvanized sheets is relatively minor because these are deeply processed steel products with high added costs and value, making the proportion of ore costs small. Additionally, the substrates for hot-dip galvanized sheets often use long-process production technologies, some of which are energy-saving compared to short-process technologies that use scrap steel and electric furnaces. However, the price increase of zinc ingots directly affects the profitability of galvanized sheets.
(3) Market Access System for Building Material Hot-Dip Galvanized Steel Sheets
.China already has product standards for building material hot-dip galvanized sheets, but given the vast size of the building materials market, many enterprises do not produce according to these standards. Unreasonably reducing the zinc layer thickness in production puts companies that adhere to standards at a competitive disadvantage, disrupts the market, harms users, and undermines national economic construction. Therefore, it is recommended that the government adopt compulsory measures to establish a market access system, especially for outdoor-use hot-dip galvanized sheets, which must be produced according to standards. Products that do not meet the standards should not be allowed into the market to ensure fair and orderly competition. Various issues in the production of hot-dip galvanized sheets will continue to be addressed; the industry should strengthen self-discipline, integrate into the international market, and seek development through competition.Steel fireproof door complianceChina already has product standards for building material hot-dip galvanized sheets, but given the vast size of the building materials market, many enterprises do not produce according to these standards. Unreasonably reducing the zinc layer thickness in production puts companies that adhere to standards at a competitive disadvantage, disrupts the market, harms users, and undermines national economic construction. Therefore, it is recommended that the government adopt compulsory measures to establish a market access system, especially for outdoor-use hot-dip galvanized sheets, which must be produced according to standards. Products that do not meet the standards should not be allowed into the market to ensure fair and orderly competition. Various issues in the production of hot-dip galvanized sheets will continue to be addressed; the industry should strengthen self-discipline, integrate into the international market, and seek development through competition.
Overview of the Manufacturing Process for Galvanized Steel Fire Doors
Galvanized steel fire doors, as a crucial component of modern building safety systems, not only possess the durability of standard steel doors but also incorporate fire-resistant capabilities. They can effectively prevent the spread of fire for a certain period, buying valuable time for evacuation and firefighting efforts. The detailed manufacturing process from material selection to final packaging is outlined below.
1. Material Selection and Procurement
- Steel Plate Selection: High-quality cold-rolled or hot-rolled steel plates are chosen as the base material for the door body, with thicknesses meeting national standards and exhibiting good mechanical properties and workability.
- Fireproof Materials: Certified fireproof core materials, such as perlite boards, vermiculite boards, or inorganic non-combustible fibers, are procured to ensure the door body maintains structural integrity at high temperatures.
- Galvanizing Materials: Hot-dip or electro-galvanized materials that meet national standards are selected for steel plate surface treatment.
- Hardware Accessories: Fire-rated locks, hinges, door closers, and other hardware are purchased to ensure the overall fire resistance is uncompromised.
2. Galvanizing Treatment for Steel Plates
- Pretreatment: The steel plate surface undergoes degreasing, derusting, and cleaning to ensure it is free of impurities.
- Galvanizing: Hot-dip or electro-galvanizing processes are applied to treat the steel plate surface, forming a uniform and dense layer of zinc to enhance corrosion resistance.
- Post-treatment: Necessary refinements are made after galvanizing to ensure the zinc layer is uniform and defect-free.
3. Fireproof Material Lamination
- Adhesive Selection: High-temperature resistant adhesives with strong bonding capabilities are chosen.
- Lamination Process: Fireproof core materials are laminated with galvanized steel plates using specialized equipment to ensure a tight bond, forming a door core panel with excellent fire-resistant properties.
4. Door Frame and Leaf Fabrication
- Cutting and Bending: Galvanized steel plates are precisely cut and bent according to design drawings to form the basic shapes of the door frame and leaf.
- Welding: High-quality welding materials and techniques are used to reinforce the door frame and leaf, ensuring structural stability.
- Grinding and Finishing: Post-welding, the surfaces are ground and finished to remove welding marks and ensure smoothness.
5. Installation of Hardware Accessories
- Positioning and Drilling: Accurate positions for hardware accessories are marked on the door frame and leaf, followed by drilling.
- Installation: Locks, hinges, door closers, and other hardware are installed according to design specifications, ensuring secure fitting and operational flexibility.
6. Quality Inspection and Testing
- Visual Inspection: The door surface is checked for scratches, unevenness, or other defects.
- Dimensional Verification: The dimensions of the door frame and leaf are measured to ensure compliance with design specifications.
- Fire Resistance Testing: National standard fire resistance tests are conducted to verify if the door meets the required fire endurance time.
- Functional Testing: The door’s opening, closing, and sealing functions are tested for normal operation.
7. Surface Coating Protection
- Primer Application: An anti-rust primer is applied to the door surface to enhance corrosion resistance.
- Paint Spraying: The surface is sprayed with paint in colors chosen by the customer or as per design requirements, enhancing aesthetics.
- Drying and Curing: The painted door is placed in a drying room for curing, ensuring strong paint adhesion and a good finish.
8. Final Assembly and Packaging
- Assembly: The door frame, leaf, and hardware accessories are assembled to ensure the door is complete and intact.
- Adjustment: The assembled fire door is adjusted to ensure tight component integration and smooth operation.
- Packaging: Waterproof, moisture-proof, and shock-resistant packaging materials are used to package the finished door, which is then labeled with tags and certification for shipment.
Through the strict control and meticulous operation of these eight major steps, galvanized steel fire doors that meet national standards and customer requirements can be produced, ensuring safety in building construction.