Innovative Steel Energy-Saving Fireproof Window and Manufacturing Process
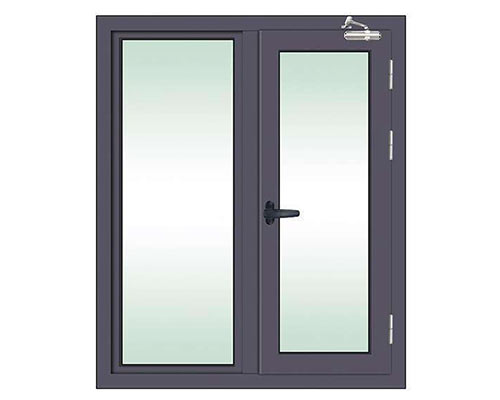
Abstract:
This invention pertains to the technical field of fireproof doors and windows, specifically introducing a unique design and manufacturing process for a steel energy-saving fireproof window. The fireproof window consists of an outer frame and an inner sash. The inner sash is equipped with double-layer glass, enhancing thermal insulation and fire resistance. Between the inner sash and the outer frame, a sliding mechanism is installed, comprising hinges equipped with torsion springs. The top of the inner sash is articulated to a first connecting plate, which rotates on one end connected to a first hinge shaft. The top of the outer frame is slidingly connected to a sliding piece, which is fixed at the bottom with a second hinge shaft.
The second hinge shaft is articulated to a second connecting plate, featuring a slotted groove for the first hinge shaft to slide through. One end of the sliding piece bends downward, where a memory metal piece and an expansion block are fixed. The memory metal piece is bent upwards and engages with a distribution slot arranged on the top of the outer frame. When the expansion block is exposed to heat, it pushes the end of the memory metal piece out of the slot, prompting the torsion spring to drive the inner sash to rotate towards the outer frame until the fireproof window closes automatically. This design is beneficial in preventing the spread of fire, thereby enhancing fire safety in buildings.
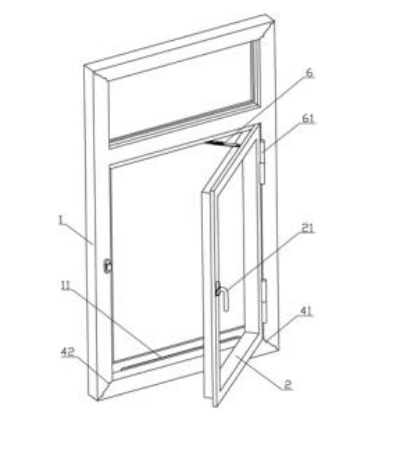
Keywords:
- Steel energy-saving fireproof window
- Manufacturing process for fireproof windows
- Double-layer glass windows
- Automatic closing fireproof window
- Fire safety solutions
- Fire-resistant construction materials
- Fire doors and windows technology
Steel Energy-Saving Fireproof Window Design and Features
- The steel energy-saving fireproof window comprises an outer frame (1) and an inner sash (2) installed on the outer frame (1). The inner sash (2) is equipped with double-layer glass (5). Notably, between the inner sash (2) and the outer frame (1), a sliding mechanism (6) is provided. This sliding mechanism (6) includes hinges (61) positioned between the inner sash (2) and the outer frame (1), with torsion springs housed within the hinges (61). The top of the inner sash (2) is hinged to a first connecting plate (62), which rotates on one end connected to a first hinge shaft (621). The top of the outer frame (1) features a sliding piece (64) that is fixed at the bottom with a second hinge shaft (632). A second connecting plate (63) is articulated on the second hinge shaft (632), incorporating a slotted groove (631) for the first hinge shaft (621) to slide through.The end of the sliding piece (64), away from the second hinge shaft (632), bends downward, where a memory metal piece (65) is fixed. The end of the memory metal piece (65), away from the second hinge shaft (632), bends upwards. The top of the outer frame (1) is arranged with multiple slots (66) for the end of the memory metal piece (65) to engage. Additionally, the end of the sliding piece (64), distant from the second hinge shaft (632), is fixed with an expansion block (68) made of heat-expandable material, positioned between the memory metal piece (65) and the outer frame (1).
- The steel energy-saving fireproof window as described in claim 1 is characterized by the end of the sliding piece (64), away from the second hinge shaft (632), being fixed with a limit post (67). The top of the limit post (67) makes contact with the underside of the memory metal piece (65), and the limit post (67) is composed of a low-melting-point material, with a melting point between 45°C and 60°C.
- According to the steel energy-saving fireproof window in claim 1, both the outer frame (1) and inner sash (2) are enclosed frames formed by multiple framing profiles. The edges of the framing profiles feature semicircular grooves (42) and semicircular blocks (41), which interlock with adjacent framing profiles.
- The steel energy-saving fireproof window in claim 3 is characterized by the inner sash (2) and outer frame (1) having multiple cavities (17) formed within their framing profiles. The sidewalls of these cavities (17) are covered with perlite (14), and some cavities (17) have sliding bases (31) connected at both ends. A steel cross post (3) is secured between these sliding bases (31), with its surface coated in a fire-retardant layer (36) made of heat-expandable material.
- In the steel energy-saving fireproof window as described in claim 4, the sliding base (31) comprises identical inner plates (311) and outer plates (312). The inner plate (311) features a cross slot (313) for the cross post (3) to pass through. Sliding blocks (32) connect between the inner plate (311) and outer plate (312). The ends of the cross post (3) are designed with symmetrical slopes, and the sliding blocks (32) create corresponding slopes on the inner side of the outer plate (312). Diagonal grooves (314) are also incorporated along the diagonal direction of the outer plate (312). A fixed block (321) that slides along with the groove (314) is secured to the surface of the sliding block (32), with a spring (315) fixed between one end of the fixed block (321) and the groove (314). The inner side of the sliding blocks (32) is affixed with sealing strips, and connecting blocks (33) are positioned between adjacent sliding blocks (32) to secure the inner plate (311) and outer plate (312). Installation grooves (37) that slide with the connecting blocks (33) are formed on the inner wall of the framing profiles.
- The steel energy-saving fireproof window in claim 1 features a drainage groove (11) formed on the outer frame (1). The drainage groove (11) extends 50%-60% of the bottom width of the outer frame (1), with a width of 3mm-4mm.
- The steel energy-saving fireproof window as stated in claim 6 has a water-absorbing cotton fabric attached to the drainage groove (11), woven from polyester fibers with irregular cross-sections.
- According to the steel energy-saving fireproof window in claim 1, a glass pressure strip (16) is fixed on the inner side of the sash’s framing profile (2), with fire-retardant cushions (15) secured at the edges of the double-layer glass (5). Weather-resistant adhesive (12) is used between the glass pressure strip (16) and the double-layer glass (5).
- A method for manufacturing the steel energy-saving fireproof window as described in any of claims 1-8 is characterized by including.
Manufacturing Process for Steel Energy-Saving Fireproof Windows
The following steps outline the manufacturing process for the steel energy-saving fireproof window:
S1. Profile Processing:
Cut each structural component to the required dimensions for the fireproof window. Following this, perform slotting and drilling operations to prepare the profiles for assembly.
S2. Internal Component Assembly:
Begin by adhering perlite (14) to the inner walls of the framing profiles. Next, sequentially insert the prepared waterproof boards (171), steel plates (172), sliding bases (31), and cross posts (3) into the framing profiles of the inner sash (2) and outer frame (1), assembling them into complete structures.
S3. Welding:
Weld the inserted steel plates (172) securely in place. Verify that the semicircular grooves (42) and semicircular blocks (41) between adjacent framing profiles fit seamlessly. After this inspection, weld the two adjacent framing profiles at their joint.
S4. Corner Treatment:
Smooth the corners and joints of the assembled inner sash (2) and outer frame (1) to ensure a clean finish.
S5. Surface Treatment:
- Remove any oil and rust from the surface of the profiles. Wash with water, then perform phosphating treatment. Rinse again and dry thoroughly.
- Blow off any dust and debris from the profile surfaces, followed by spraying a protective coating onto the profiles.
- Cure the applied coating to form a protective layer.
S6. Glass Installation:
Carefully install the double-layer glass (5) into the inner sash (2) framing, ensuring a proper sealing treatment to enhance fire resistance.
S7. Accessory Installation:
Install the necessary hardware components for the fireproof window into the pre-drilled slots and holes prepared in step S1.
S8. Assembly Method for Sliding Base and Cross Post:
As detailed in claim 9, within step S2, the sliding base (31) and cross post (3) should be pre-assembled before being inserted into the framing profiles of the inner sash (2) and outer frame (1). The assembly procedure is as follows:
- a. Utilize connecting blocks (33) to slide-fit one sliding base (31) into one end of the framing profile.
- b. Insert the cross post (3) from the opposite end of the framing profile, ensuring the end of the cross post (3) engages with the cross slot (313) until the sealing strip on the sidewall of the sliding block (32) tightly contacts the inner wall of the framing profile.
- c. Finally, install the second sliding base (31) at the opposite end of the framing profile, ensuring that the sealing strip on this sliding base (31) also contacts the inner wall firmly.
Technical Field
[0001] This invention pertains to the field of fireproof doors and windows, specifically focusing on a steel energy-saving fireproof window and its manufacturing process.
Background Technology
[0002] As living standards continue to improve, the demand for energy efficiency and thermal insulation in buildings has risen significantly. Simultaneously, the awareness of fire safety performance in homes has grown, particularly due to the increasing frequency of building fires that have drawn attention from both the public and fire departments. For high-rise buildings, appropriate fire safety measures should be integrated into the design process to prevent fires and mitigate their potential harm to life and property. Fireproof windows serve as a common fire-resistant architectural structure, typically composed of an outer frame, an inner sash, and fireproof glass, with fire-resistant materials filling the frame to isolate and prevent the spread of flames. Fireproof windows are generally installed on exterior walls to separate indoor spaces from the external environment.
Invention Content
[0004] In response to the deficiencies of existing technologies, the primary objective of this invention is to provide a steel energy-saving fireproof window that can automatically close, thus cutting off air circulation and hindering the spread of fire.
The steel energy-saving fireproof window comprises an outer frame and an inner sash installed within the outer frame, featuring double-layer glass. A push-pull assembly is located between the inner sash and the outer frame. This push-pull assembly includes hinges installed between the inner sash and the outer frame, equipped with torsion springs. The top of the inner sash is hinged to a first connecting plate, with the opposite end of the first connecting plate rotatably connected to a first hinge shaft. The top of the outer frame is slidably connected to a sliding piece, the bottom of which is fixed with a second hinge shaft. The second hinge shaft is hinged to a second connecting plate that has a slot for the first hinge shaft to slide within. The end of the sliding piece, away from the second hinge shaft, bends downwards and is fixed with a memory metal piece. The end of the memory metal piece, opposite the second hinge shaft, bends upwards, while multiple slots are evenly distributed along the top of the outer frame to accommodate the ends of the memory metal pieces. Additionally, an expansion block made of thermally expanding materials is fixed at the end of the sliding piece, positioned between the memory metal piece and the outer frame. [0006] With this arrangement, when the window is opened regularly, the first connecting plate moves the second connecting plate inward, causing the sliding piece to slide along the outer frame under the influence of the second hinge shaft. When the end of the memory metal piece engages with a slot, the position of the inner sash is secured, allowing for angle adjustment of the inner sash’s opening. When the expansion block is heated, it increases in volume, pushing the end of the memory metal piece out of the slot. At this moment, the torsion spring installed at the hinge drives the inner sash to rotate towards the outer frame until it closes, effectively creating an automatic closing mechanism for the fireproof window that prevents external air from entering, thereby helping to contain the spread of fire. [0007] Furthermore, the sliding piece is designed to have a limiting column fixed at the end farthest from the second hinge shaft. The top of this limiting column contacts the underside of the memory metal piece, and the limiting column is made of a low-melting-point material with a melting point between 45 and 60 degrees Celsius.
[0008] By implementing the above technical solution, during routine use, the limiting column remains solid, providing a limiting function for the memory metal piece to prevent excessive deformation that could hinder recovery, ensuring the normal operation of the push-pull assembly. In the event of a fire, as indoor temperatures rise, the limiting column melts without affecting the expansion, allowing the end of the memory metal piece to be pushed out of the slot, thereby ensuring the automatic closing function of the fireproof window.
[0009] Furthermore, the outer frame and inner sash are designed as closed frames composed of multiple border profiles. The edges of the border profiles feature semi-circular grooves and semi-circular blocks, which fit together seamlessly between adjacent border profiles.
[0010] This configuration enhances the assembly of adjacent border profiles, as the matching of the semi-circular grooves and blocks provides guidance, allowing operators to align the profiles accurately, while also improving the sealing between the adjacent border profiles.
[0011] Additionally, multiple cavities are formed within the border profiles of the inner sash and outer frame. The cavity sidewalls are covered with perlite, and some cavities are connected at both ends to sliding bases. Steel cross pillars are engaged between the sliding bases, and the surface of the cross pillars is coated with a flame-retardant layer made from heat-expandable materials.
[0012] This technical solution enhances the strength of the outer frame and inner sash through the use of steel cross pillars, making the fireproof window more resistant to deformation caused by fire exposure. The flame-retardant layer, made from heat-expandable materials, expands when exposed to fire, pressing against the inner walls of the border profiles to absorb heat from both the outer frame and inner sash, thus increasing the fire resistance of the window.
[0013] The sliding base consists of identical inner and outer plates, with the inner plate featuring a cross slot for the cross pillar to pass through. Four sliding blocks are connected to slide between the inner and outer plates. The ends of the cross pillar are shaped with symmetrical slopes, and the sliding blocks form corresponding slopes on their sides, with slanted grooves cut into the outer plate along its diagonal. A fixed block that interacts with the slanted grooves is attached to the surface of the sliding block, and a spring is fixed between the fixed block and one end of the slanted groove. Sealing strips are attached to the sides of the sliding blocks that face the inner walls of the border profiles, and connecting blocks are positioned between adjacent sliding blocks to secure the inner and outer plates. An installation slot compatible with the connecting blocks is formed on the inner wall at the ends of the border profiles.
[0014] This configuration ensures that when the cross pillar is inserted into the cross slot on the inner plate, the sloped end of the cross pillar engages with the slope of the sliding block. This interaction pushes the sliding block along the slanted groove, thereby pressing it tightly against the inner wall of the border profile. The sealing strip on the side of the sliding block closes any gaps between the sliding base and the inner wall of the border profile, enhancing the airtightness of the outer frame and inner sash. This helps to minimize air movement between the inside and outside of the fireproof window, thus aiding in fire prevention.
[0015] Furthermore, a drainage slot is provided on the outer frame, with a length constituting 50%-60% of the width of the outer frame’s bottom and a slot width of 3mm-4mm.
[0016] This arrangement of the drainage slot, with a width of 3mm-4mm, prevents outdoor debris from easily entering the outer frame due to its smaller size. The elongated drainage slot increases drainage capacity, ensuring effective water drainage while minimizing any impact on the strength of the outer frame.
[0017] Additionally, the drainage slot is bonded with water-absorbing cotton fabric, woven from polyester fibers with irregular cross-sections.
[0018] This configuration utilizes the unique cross-sectional shape of the polyester fibers in the water-absorbing cotton fabric, allowing for rapid absorption of moisture within the outer frame due to the grooves in the fiber surfaces. This moisture is then spread out to facilitate quick evaporation, effectively preventing moisture retention on the outer frame surface that could lead to corrosion.
[0019] The surface of the inner sash’s inner border profile is fixed with a glass pressing strip.
[0020] The edges of the glass are secured with flame-retardant pads, and a weather-resistant adhesive is filled between the glass pressing strip and the double-layer glass.
[0021] The second objective of this invention is to provide a manufacturing method for the steel energy-saving fireproof window, comprising the following steps:
- S1. Profile Processing: Cut each structural component to the required dimensions of the fireproof window, followed by grooving and drilling operations.
- S2. Internal Component Assembly: First, adhere perlite to the inner walls of the border profiles, then sequentially insert the prepared waterproof board, steel plates, sliding bases, and cross pillars into the inner sash and outer frame’s border profiles to assemble the complete inner sash and outer frame.
- S3. Welding: First, weld the inserted steel plates to secure them, then inspect for seamless jointing between the semi-circular grooves and blocks of adjacent border profiles. Next, weld the adjacent border profiles along their joining seams.
- S4. Corner Treatment: Grind and smooth the corners and joints of the assembled inner sash and outer frame.
- S5. Surface Treatment:
- (1) Remove oil and rust from the profile surfaces, wash them with water, perform phosphating treatment, then wash and dry again.
- (2) Blow away dust and debris from the profile surfaces, followed by spray coating with paint.
- (3) Bake the paint to cure and form a protective layer.
- S6. Glass Installation: Insert the double-layer glass into the inner sash frame and perform sealing treatment.
- S7. Accessory Installation: Install the required hardware accessories into the slots and holes prepared in step S1.
[0022] The method further specifies that in step S2, the sliding bases and cross pillars should be assembled before being inserted into the inner sash and outer frame’s border profiles. The assembly process is as follows:
- a. First, install one sliding base at one end of the border profile using a connecting block that slides into the installation groove.
- b. Next, insert the cross pillar from the opposite end of the border profile, ensuring the end of the cross pillar fits into the cross slot until the sealing strip on the sliding block tightly contacts the inner wall of the border profile.
- c. Finally, install the other sliding base at the opposite end of the border profile, ensuring the sealing strip on this sliding base also contacts the inner wall.
[0023] In summary, the beneficial technical effects of this invention include:
- In this scheme, when the expansion block encounters heat, it pushes the end of the memory metal piece out of the slot, allowing the torsion spring to drive the inner sash to rotate towards the outer frame until the fireproof window is closed, achieving an automatic closing effect that helps to restrain the spread of fire.
- In this scheme, during normal use, the limiting column remains solid and limits the memory metal piece to prevent excessive deformation that could hinder recovery, ensuring the normal operation of the push-pull assembly. In the event of a fire, as indoor temperatures rise, the limiting column melts, allowing the memory metal piece to be released from the slot, thus ensuring the automatic closing function of the fireproof window.
- This scheme employs water-absorbing cotton fabric woven from polyester fibers with irregular cross-sections. The grooves on the surface of the polyester fibers quickly absorb moisture within the outer frame and disperse it to facilitate rapid evaporation, effectively preventing moisture retention that could lead to corrosion of the outer frame.
Description of the Drawings: [0024] Figure 1 is a schematic diagram of the overall structure of Example 1;
Figure 2 is a cross-sectional structural diagram of Example 1 in the closed position.
[0024] Figure 3 illustrates an exploded structural view of the outer frame in Example 1;
Figure 4 illustrates an exploded structural view of the push-pull assembly in Example 1.
[0025] Reference Marks:
- Outer Frame;
- 11. Drainage Slot;
- Weather-Resistant Adhesive;
- Perlite;
- Flame-Retardant Pad;
- Glass Pressing Strip;
- Cavity;
- Waterproof Board;
- Steel Plate;
- 11. Drainage Slot;
- Inner Sash;
- 21. Handle;
- Cross Pillar;
- 31. Sliding Base;
- 311. Inner Plate;
- Outer Plate;
- Cross Slot;
- Sloping Slot;
- Spring;
- 311. Inner Plate;
- Sliding Block;
- Fixed Block;
- Connecting Block;
- Flame-Retardant Layer;
- Installation Slot;
- Semi-Circular Block;
- Semi-Circular Groove;
- 31. Sliding Base;
- Double-Layer Glass;
- Push-Pull Assembly;
- 61. Hinge;
- First Connecting Plate;
-
- First Hinge Axis;
- Second Connecting Plate;
- Long Slot;
- Second Hinge Axis;
- Sliding Piece;
- Flange;
- Sliding Slot;
- Memory Metal Piece;
- Slot;
- Limiting Column;
- Expansion Block.
Specific Implementation: [0026] Below is a detailed description of the invention in conjunction with the accompanying drawings.
[0027] Example 1: As shown in Figure 1, the steel energy-saving fireproof window comprises an outer frame (1) and an inner sash (2), both constructed from multiple border profiles forming a rectangular closed frame, with one side of the inner sash (2) hinged to the outer frame (1). Each border profile is equipped with a semi-circular groove (42) and a semi-circular block (41), ensuring a complementary fit between adjacent border profiles.
[0028] As shown in Figures 1 and 2, the inner sash (2) is fitted with double-layer glass (5), and the surface of the inner sash (2) border profile is secured with a glass pressing strip (16). The edges of the double-layer glass (5) are fixed with flame-retardant pads (15), and a weather-resistant adhesive (12) fills the space between the glass pressing strip (16) and the double-layer glass (5). The weather-resistant adhesive (12) has undergone accelerated artificial weathering tests, showing no significant changes in physical and chemical properties, demonstrating excellent weathering resistance and high/low-temperature performance. The flame-retardant pad (15), made from flame-retardant materials, also exhibits outstanding durability in various temperature conditions.
[0029] The outer frame (1) features a drainage slot (11) that spans 50%-60% of the width of the outer frame (1) at the bottom, with a slot width of 3mm-4mm. The smaller slot width prevents debris from entering the outer frame (1) while the elongated drainage slot (11) allows for effective drainage capacity without compromising the structural integrity of the outer frame (1). Additionally, a water-absorbing cotton fabric is adhered to the drainage slot (11). This fabric is woven from polyester fibers with irregular cross-sections, featuring grooves that enhance moisture absorption and facilitate rapid evaporation, thus providing excellent drainage performance.
[0030] As shown in Figures 1 and 3, a push-pull assembly (6) is installed between the inner sash (2) and the outer frame (1). The push-pull assembly (6) includes hinges (61), a first connecting plate (62), a second connecting plate (63), and a sliding piece (64). The hinge (61) is installed between the inner sash (2) and the outer frame (1) to facilitate rotation, and it is equipped with a torsion spring to enable automatic closing of the inner sash (2). The first connecting plate (62) is hinged at one end to the top of the inner sash (2), while its other end connects to a first hinge axis (621) that slides within a long slot (631) on the second connecting plate (63). The second connecting plate (63) is hinged at its end opposite the first connecting plate (62) to a second hinge axis (632), with the top of this hinge axis fixed to the bottom of the sliding piece (64).
The sliding piece (64) is a flat element that bends downward at its end away from the second hinge axis (632) and is affixed with a memory metal piece (65). The memory metal piece (65) possesses an automatic reset function. The top of the outer frame (1) has a sliding slot (642) that aligns with the width direction of the outer frame (1). Flanges (641) are fixed on both sides of the sliding piece (64) to enable smooth movement within the sliding slot (642). Multiple slots (66) are evenly distributed along the width of the outer frame (1) on the underside of the top surface. The end of the memory metal piece (65) away from the second hinge axis (632) curves upwards to fit into the slots (66). Furthermore, the end of the sliding piece (64) opposite the second hinge axis (632) is fixed with an expansion block (68) and a limiting column (67). The expansion block (68) is made from a heat-expandable material.
[0031] The memory metal piece (65) is positioned between the sliding piece (64) and the outer frame (1). The limiting column (67) is made of a low melting point material, which remains solid at room temperature but transitions to a liquid state at temperatures above 50 degrees Celsius. In this example, the limiting column (67) is constructed from paraffin wax, which has a melting point of approximately 48 degrees Celsius.
[0032] As shown in Figures 1 and 2, both the outer frame (1) and the inner sash (2) feature hollow border profiles that contain multiple cavities (17). The side walls of these cavities (17) are covered with perlite (14), and some cavities (17) are equipped with sliding bases (31) and cross pillars (3). Referring to Figure 4, the sliding bases (31) are installed at both ends of the border profiles, comprising an inner plate (311) and an outer plate (312), both of which are identical in shape and size. The inner plate (311) is located between the outer plate (312) and the steel liner. The inner plate (311) has a cross-shaped slot (313), and the cross pillar (3) is a columnar structure with a cross-section, featuring symmetrical sloping surfaces at its ends that fit snugly within the cross slot (313).
Close to the double-layer glass (5), the cavities (17) are filled with a waterproof board (171) and a steel plate (172). The waterproof board (171) prevents moisture from spreading into the cavity (17), while the steel plate (172) provides structural support, enhancing the strength of both the outer frame (1) and the inner sash (2).
[0033] As shown in Figure 4, four sliding blocks (32) are positioned between each outer plate (312) and inner plate (311). The sliding blocks (32) are rectangular and are adhered with sealing strips on the side facing the inner wall of the border profiles. The surfaces of the outer plate (312) feature four sloping slots (314), oriented in the same diagonal direction as the outer plate (312). These sloping slots (314) are uniformly and symmetrically distributed. Each sliding block (32) has a fixed block (321) attached to the surface that contacts the outer plate (312), which slides within the sloping slots (314). A spring (315) is fixed between one end of the fixed block (321) and the sloping slot (314). Connecting blocks (33) are placed between adjacent sliding blocks (32) to secure the inner plate (311) and outer plate (312), while installation slots (37) are located on the inner wall at the ends of the border profiles to slide fit with the connecting blocks (33).
When the cross pillar (3) is inserted into the cross slot (313) on the inner plate (311), the sloping surface at the end of the cross pillar (3) makes contact with the corresponding sloping surface on the sliding block (32). The cross pillar (3) pushes the sliding blocks (32) to slide along the sloping slots (314), pressing the sliding blocks (32) against the inner wall of the border profile. The sealing strips on the side of the sliding blocks (32) seal the gap between the inner wall of the border profile and the sliding base (31), enhancing the airtightness of both the outer frame (1) and the inner sash (2). This effectively reduces air movement between the interior and exterior of the fireproof window, aiding in fire prevention.
[0034] The surface of the cross pillar (3) is covered with a flame-retardant layer (36), which is made from heat-expanding materials that adhere tightly to the inner wall of the border profile when exposed to fire. In normal use, when opening the window, the user simply holds the handle (21) to rotate the inner sash (2). The first connecting plate (62) then moves the second connecting plate (63) inward, causing the sliding piece (64) to glide along the outer frame (1). When the end of the memory metal piece (65) away from the second hinge axis (632) engages with the slots (66), the position of the inner sash (2) is fixed. The slots (66) are evenly distributed along the top of the outer frame (1), allowing for angle adjustment of the inner sash (2).
[0035] In the event of a fire, as the indoor temperature rises, the limiting column (67) on the sliding piece (64) melts, and the expansion block (68) expands due to heat, pushing the end of the memory metal piece (65) out of the slots (66). This action causes the torsion spring at the hinge (61) to drive the inner sash (2) to rotate towards the outer frame (1) until it fully closes, automatically sealing the fireproof window. This mechanism effectively prevents external air from entering, helping to contain the spread of fire.
[0036] Example 2: As illustrated in Figures 1-4, a method for manufacturing the steel energy-saving fireproof window includes the following steps:
- S1. Profile Processing: Cut all structural components to the required dimensions for the fireproof window, followed by slotting and drilling operations.
- S2. Internal Assembly: First, use fire-resistant adhesive to secure the perlite (14) to the inner walls of the border profiles. Then sequentially fill the waterproof board (171), steel plate (172), sliding bases (31), and cross pillars (3) into the various cavities (17) of the inner sash (2) and outer frame (1) to assemble complete inner and outer frames.
- The assembly process for the sliding bases (31) and cross pillars (3) before filling them into the cavities (17) involves:
- a. First, install one sliding base (31) at one end of the cavity using the connecting block (33) in sliding fit with the installation slot (37).
- The assembly process for the sliding bases (31) and cross pillars (3) before filling them into the cavities (17) involves:
b. Next, insert the cross pillar (3) from the opposite end of the cavity, ensuring that the end of the cross pillar (3) fits into the cross slot (313) until the sealing strip on the side of the sliding block (32) is tightly pressed against the inner wall of the cavity.
c. Then, install the second sliding base (31) at the opposite end of the cavity, ensuring that the sealing strip on this sliding base (31) also firmly contacts the inner wall of the cavity. After this, assemble all border profiles to complete the inner sash (2) and outer frame (1).
S3. Welding: First, weld the inserted steel plate (172) in place, then check that the semicircular grooves (42) and semicircular blocks (41) between adjacent border profiles are seamlessly connected. Following this, weld the adjacent border profiles along their joint areas.
S4. Corner Treatment: Polish the corners and joints of the assembled inner sash (2) and outer frame (1).
S5. Surface Treatment:
- (1) Use an alkaline solution to remove oil and rust from the surface of the profiles, followed by rinsing with water. Then, perform phosphating treatment, rinse again, and dry.
- (2) Blow away dust and debris from the surface of the profiles, and then spray paint onto the profile surfaces.
- (3) Bake the sprayed paint in an oven to create a protective coating on the profile surfaces.
S6. Glass Installation: Insert the double-layer glass (5) into the frame of the inner sash (2) and ensure it is sealed properly.
S7. Accessory Installation: Install the necessary hardware accessories for the fireproof window into the grooves and holes prepared in step S1.
[0036] In the above step S2, the perlite expands into a lightweight, multifunctional new material characterized by low apparent density, low thermal conductivity, good chemical stability, non-toxicity, odorlessness, fire resistance, and sound absorption properties. The adhesion of a layer of perlite to the inner walls of the border profiles effectively enhances the fire resistance and sound insulation of the fireproof window.
[0037] In the aforementioned step S5, phosphating is the central aspect of pre-treatment for coating. The metal workpiece is treated with phosphoric acid solutions containing manganese, zinc, and cadmium salts to form an insoluble phosphate protective film on the profile surfaces. This phosphate film has a dense structure with microscopic pores that increases the surface area of the profiles, enhancing the contact area for the coating. This interaction promotes beneficial infiltration between the phosphate film and the coating, significantly improving the adhesion of organic coatings to the profiles. The phosphate film forms a stable, non-conductive barrier, transforming the metal surface from a good conductor to a poor conductor, thereby suppressing microbattery formation and preventing coating corrosion.
[0038] The above is merely a preferred embodiment of the present invention. The scope of the invention is not limited to the above embodiments; any technical solutions within the spirit of the present invention shall be included in the protection scope of this invention. It should be noted that any modifications and refinements that do not deviate from the principles of this invention, as understood by those skilled in the art, should also be considered within the scope of this invention’s protection.
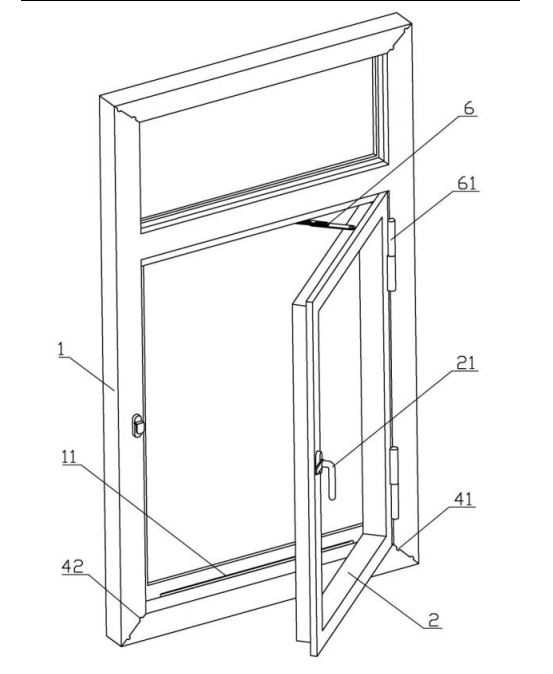
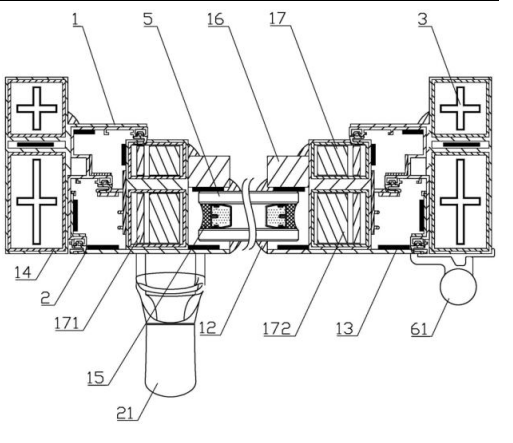
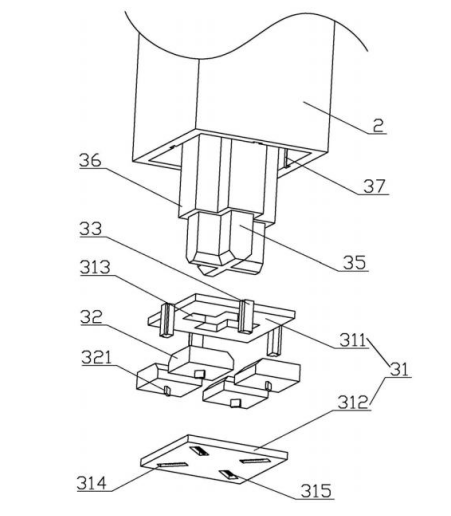