We are a top fireproof door manufacturer in China and would like to share some useful knowledge about fireproof doors. This is a practical blog that shares the production process diagram of fire doors, with sufficient theoretical basis and strong practical significance. It can be applied to most standard fire door manufacturing processes, hoping to be helpful to the construction industry.Steel fire proof door production process.
Steel fire proof door production process
1, steel fire door production process
1.1 Production process flow chart of door frame:
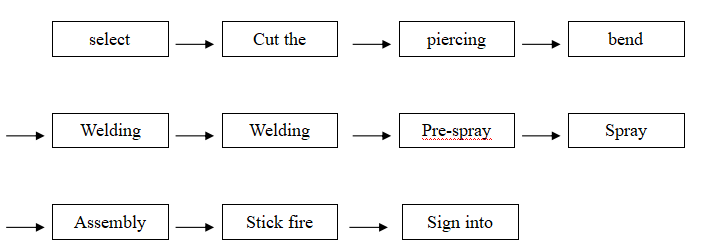
1.2 Flow chart of door production process:
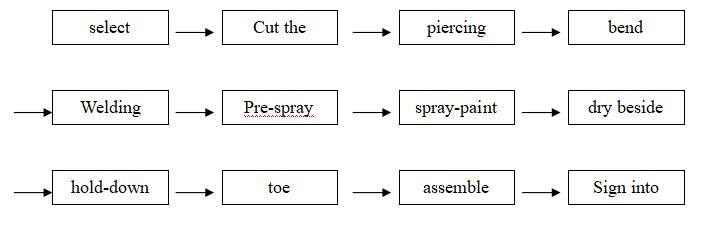
2, steel fire proof door production process standard
2.1. Production process standard of door frame
order number | project name | Process standards and requirements | remarks | |
1 | select materialRaw material quality reinspection | The galvanized surface coating is uniform, smooth surface without convex, crease and rust; the plate thickness tolerance is ± 0.06mm | The material shall be confirmed according to the material sheet, but the plate thickness and surface quality shall be rechecked | |
2 | Cut the plate and lower the material | 1. The size and accuracy shall be made according to meeting the requirements of the drawings | ||
2. Diagonal dimension difference is 2 mm; length dimension difference ± 1mm; width dimension difference ± 1mm | ||||
3, the parts shall not have flying edge, burrs, creases and other defects | ||||
3 | Lock hole and pin hole, etc | The size and accuracy shall be made according to the drawings | ||
2. The hole (groove) shall not have the defects; remove the burr after punching (groove) | ||||
4 | Bend forming | 1. The dimensions shall be made according to the drawing requirements | ||
Bend vertical: 90 °± 0.5° | ||||
The width difference of door frame is ± 1mm | ||||
5 | Welding lining plate(Hinge and door er) | Dimensions are made according to the drawing requirements | ||
The left and right position of the reinforcement plate is 1.5 mm | ||||
3. The upper and lower position of the reinforcing board is 2 mm | ||||
4, remove the burr, leveling | ||||
5. The position deviation of the reinforcing plate is 0.5mm | ||||
6. Spot welding around the reinforcement plate, the spacing between the solder joints is 20~30mm, the unilateral solder joints shall not be less than 3 points, the welding shall be firm, and the solder joints shall not have defects such as false welding and burning | ||||
6 | Combination door frame | 1. The dimensions shall be made according to the drawing requirements | ||
2. The welding plane interface shall be full welding, polished and polished after welding, without false welding, burning through, air hole and other defects | ||||
3. In other positions, the distance between the solder joints is 4~6mm, the unilateral solder joints shall not be less than 3 points, the welding is firm, and the solder joints shall not have false welding, burning through and other defects | ||||
dimensional tolerance | Cutting mouth height inside the door frame | 0~﹢1mm | ||
Cutting mouth width inside the door frame | 0~﹢1mm | |||
geometric tolerance | Two diagonal length difference in the door frame | ≤2mm | ||
The verticality of the front and side facades of the door frame | ≤1.5mm | |||
7 | Pre-injection molding treatment | 1, grinding all solder joints, plane welding to be flat, smooth | ||
2, the surface of oil removal, rust clean, door frame cleaning treatment | ||||
3, the atomic ash at the gap | ||||
8 | Surface spray plastic powder | 1. The spraying process can be transferred after passing the inspection | ||
2. Plastic spraying: adjust the color according to the contract or / and user requirements, and the plastic spraying layer is uniform, smooth, smooth, without piles, hemp points and bubbles, etc | ||||
3. The baking temperature is ± 20℃ according to the temperature requirement of the plastic powder. After baking, the surface is smooth and smooth, the color is bright, and the spraying layer is firm and without defects | ||||
9 | Assemble fire hinge | 1. The assembly size shall be prepared according to the drawings | ||
2, the fire hinge can support the weight of the door body and should rotate flexibly | ||||
The clearance between door frame and door frame is not more than 4mm | ||||
10 | Install fire rubber strip | 1. Fire proof tape shall be used in accordance with the consistency requirements | ||
2, the slot inside the door frame paste fire proof tape | ||||
11 | Install age at the top of door frame | 1. The assembly size shall be prepared according to the drawings | ||
2, the sign with rivevet fixed, riveting firmly, reliable | ||||
3, the installation position shall not be deviated, and the sign shall be consistent with the door frame performance requirements | ||||
12 | Sign into the warehouse | 1. Place the PVC protective belt on the outer surface of the door frame | ||
2. After the door box is qualified, paste the label, indicate the site name, direction, model and category, and mark the storage |
2.2 Production process standard of door fan
order number | project name | Process standards and requirements | remarks | |||
1 | select materialRaw material quality reinspection | The galvanized surface coating is uniform, smooth surface without convex, crease, rust, etc defects; the plate thickness tolerance is ± 0.06mm | The material shall be confirmed according to the material sheet, but the plate thickness and surface quality shall be rechecked | |||
2 | Cut the plate and lower the material | 1. The size and accuracy shall be made according to meeting the requirements of the drawings | ||||
2. Diagonal dimension difference is 2 mm; length dimension difference ± 1mm; width dimension difference ± 1mm | ||||||
3, the manufactured parts shall not have flying edge, burrs, creases and other defects | ||||||
3 | Punch (trough), etc | The size and accuracy shall be made according to the drawings | ||||
2. The hole (groove) shall avoid the defects; remove the burr after punching (groove) | ||||||
4 | Bend forming | 1. The dimensions shall be made according to the drawing requirements | ||||
2. Bend verticality: 90 °± 0.5° | ||||||
3. The size difference of the door panel height is ± 1mm | ||||||
4, the door panel width and size difference is ± 1mm | ||||||
5. The two-diagonal length difference of the door panel is 2mm | ||||||
6. Size difference of other accessories is ± 1mm | ||||||
5 | Panel group welding | Point welding edge bar | Spot welding machine spot welding, welding firm, welding joints shall not have false welding, burning through and other defects, the spot welding spacing is 200~300mm | |||
Group welding door lockStrengthening frame (plate) | Dimensions are made according to the drawing requirements | |||||
The left and right position of the reinforcement plate is 1.5 mm | ||||||
3. The upper and lower position of the reinforcing board is 2 mm | ||||||
4, remove the burr, leveling | ||||||
5. The position deviation of the reinforcing plate is 0.5mm | ||||||
6, use the electric welding machine for spot welding around the reinforcing plate, the spacing between solder joints is 50~100mm, the unilateral solder joints shall not be less than 3 points, welding is firm, the solder joints shall not have defects such as false welding, burning and on | ||||||
Group welding of the hinge reinforcing plate | Dimensions are made according to the drawing requirements | |||||
The left and right position of the reinforcement plate is 1.5 mm | ||||||
3. The upper and lower position of the reinforcing board is 2 mm | ||||||
4, remove the burr, leveling | ||||||
5, with the electric welding machine along the reinforcement plate peripheral spot welding, the solder joint spacing is 20~30mm, unilateral solder joints shall not be less than 3 points, welding firm, solder joint shall not have false welding, burning and other defects | ||||||
6 | Combination skeleton | 1. The dimensions shall be made according to the drawing requirements | ||||
2. The welding plane interface shall be full welding, polished and polished after welding, without false welding, burning through, air hole and other defects | ||||||
3. In other positions, the distance between the solder joints is 4~6mm, the unilateral solder joints shall not be less than 3 points, the welding is firm, and the solder joints shall not have false welding, burning through and other defects | ||||||
dimensional tolerance | Skeleton height | -1~﹢1mm | ||||
Skeleton width | -2~﹢1mm | |||||
geometric tolerance | Two-diagonal length difference of the skeleton | ≤2mm | ||||
7 | Pre-injection molding treatment | 1, grinding all solder joints, plane welding to be flat, smooth | Front and rear door panels, edge, fire glass pressure frame | |||
2, the surface of oil removal, rust clean, the door plate clean treatment | ||||||
8 | Surface spray plastic powder | 1. The front and rear door panels can be transferred only after passing the manufacturing inspection | Front and rear door panels, edge, fire glass pressure frame | |||
2. Plastic spraying: adjust the color according to the contract or / and user requirements, the spraying layer is uniform, smooth, smooth, without stacking, hemp and bubbles, etc. (the same door frame) | ||||||
The baking temperature is ± 20℃ according to the temperature requirement of the plastic powder. After baking, the surface is smooth and smooth, and the color is bright, and the coating layer is firm and without defects | ||||||
9 | Fill the inner filling material | 1. Make the adhesive bonding combination skeleton on the back panel according to the requirements of the drawings | ||||
2, cold press plate, pressure of 6 mpa, time for 4-6 hours | ||||||
3. Fill the perlite / vermiculite filling material in the rear panel assembly, the filling density meets the specified requirements, the hot press plate, the pressure is 10 mpa, and the time is 0.5-1 hour | ||||||
Test whether the filling density of the filling material meets the specified requirements | ||||||
10 | clamping kit | platen | 1 front panel inner plane coated with adhesive, scrape flat, uniform, front panel and rear panel assembly buckle, | |||
2, cold press plate, pressure is 8 mpa, time is 8-10 hours | ||||||
Group afterDoor plate accuracy | 1. The height size difference of the front and rear panels is ± 1mm | |||||
2, the door panel height direction bending 2 <‰ | ||||||
3, the door panel width direction bending 2 <‰ | ||||||
Door panel distortion of 3mm | ||||||
The two-diagonal length difference of the door panel is 2.5mm | ||||||
11 | Welding of the plate plate welded | The spacing between solder joints is uniform and not greater than 200mm, welding is firm, welding joints shall not have any defects, and smooth smooth after welding | ||||
12 | Door fan package edge | 45° No obvious joint gap at the interface, no burr, and no damage to the plastic powder surface at the joint. The fastening screws are not greater than 300mm apart and arranged along the width of the door plate | ||||
Assemble fire hinge | Assembly dimensions shall be prepared according to the drawing requirements | |||||
2, the fire hinge can support the weight of the door body and should rotate flexibly | ||||||
The clearance between door frame and door frame is not more than 4mm | ||||||
4. The fitting gap between the door fan and the door frame hinge is not more than 2mm | ||||||
5. The gap between the opening edge of the door is not more than 3mm with the door frame in the closing state | ||||||
11 | Sign into the warehouse | After the door inspection is qualified and correct, paste the label, indicate the site name, opening direction, model, type and type, and mark the storage |