Understanding the Production Process of Fire Door Frames
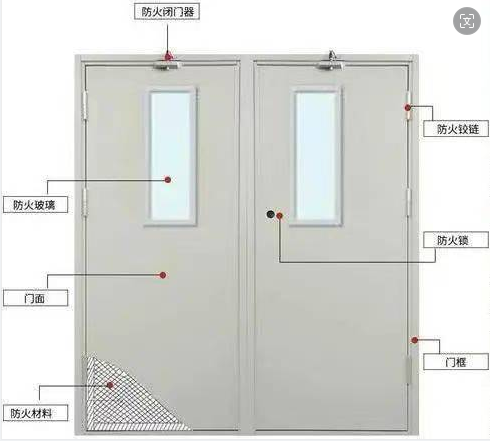
As a leading fire door manufacturer in China, Henan YK Door Industry Co., Ltd. emphasizes the importance of a rigorous production process to ensure the highest safety standards in our fire door frames. Here, we break down the steps involved in the manufacturing of our high-quality fire door frames, which are essential for maintaining safety in various buildings.The production of fireproof door frames includes material cutting, forming, welding, and finishing to ensure durability and fire resistance.
UL Fire Door Frame Standards
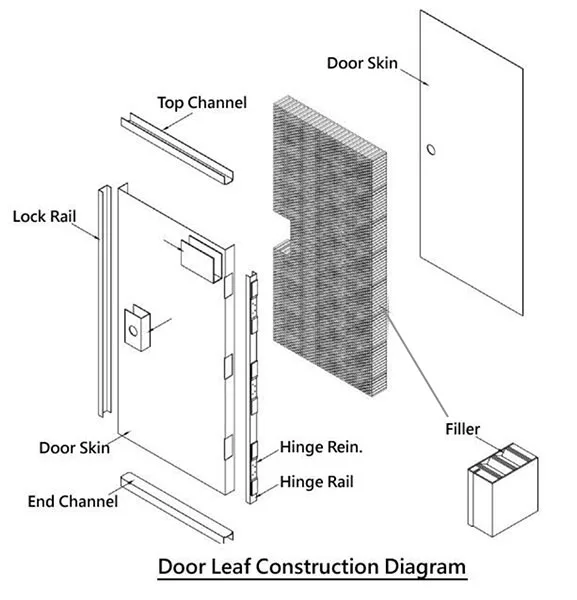
UL-certified fire door frames must be constructed from cold-rolled galvanized steel (G90 coating, ≥1.6mm thickness) with continuous welding for seamless integrity. The frame cavity requires mineral wool or ceramic fiber infill (density ≥110kg/m³), tested to UL 10B/NFPA 80 standards. A ≤3mm expansion gap between frame and wall, paired with intumescent seals, ensures flame-blocking performance under extreme heat without structural deformation.
Step-by-Step Production Process
- Wood Drying: The initial step involves drying the wood to reduce moisture content, ensuring durability and stability in the final product.production process of fireproof door frames.
- Processing into Specifications: Once dried, the wood is processed into specified dimensions suitable for fire door frame construction.
- Flame Retardant Impregnation: The specified wood undergoes flame retardant impregnation. For Grade A fire doors, a minimum of 110 kg of solid flame retardant is required per cubic meter of wood, while Grade B fire doors require at least 90 kg.
- Secondary Drying: The impregnated wood is subjected to a secondary drying process to ensure the effectiveness of the flame retardant treatment.
- Precision Machining: The flame-retardant-treated wood is then precision machined, involving sanding, routing, mortising, drilling, and the installation of expansion fire seals.
- Inspection, Packaging, and Storage: The final step involves inspecting the frames, packaging them appropriately, and storing them until delivery.
Production Process for Fire Door Leaves
The production process for fire door leaves follows similar steps:
- Wood Drying: Just like frames, wood for door leaves must be dried thoroughly.
- Processing into Specifications: The dried wood is shaped into specified dimensions.
- Flame Retardant Impregnation: The same impregnation treatment is applied, with solid flame retardant requirements matching those for door frames.
- Secondary Drying: The impregnated wood undergoes a second drying phase.
- Precision Machining: The processed wood is precision machined into components, including frame structures.
- Filling Insulation: The frame is filled with aluminosilicate fiber blanket or rock wool board, followed by applying high-temperature adhesives and installing aluminosilicate fiber mats.
- Assembly: Components such as the door leaf framework and outer panels are assembled.
- Pressing: The assembled door leaves are then shaped using hot or cold press machines.
- Final Adjustments: Width and length adjustments are made for a perfect fit.
- Sealing Edges: The edges are sealed with flame-retardant-treated wood.production process of fireproof door frames.
- Final Inspection: The door leaves undergo a final sanding and inspection before storage.
Challenges in Current Production Techniques
While our current processes are efficient, several challenges persist:
- Long Drying Times: Secondary drying times for fire door frames can take 30 to 45 days, impacting overall production timelines.
- Structural Adjustments: To prevent flame or smoke penetration, the framework must be intricately designed, requiring additional processing time.
- Material Strength: The aluminosilicate fiber mats require additional support due to their low strength, typically needing metal reinforcements.
- Wood Utilization: Current practices often lead to low wood utilization rates, particularly with decorative materials.
Innovations in Fire Door Production
Recent advancements in our production methods have addressed these challenges:
- Efficient Flame Retardant Treatment: By focusing on the edge banding materials, we significantly reduce processing times for flame retardant treatment and secondary drying, leading to a more streamlined production cycle.
- Material Optimization: Using pine or engineered wood for internal frame materials allows us to maintain high strength while minimizing waste and costs.
- Improved Assembly Techniques: Our assembly sequence enhances efficiency by compressing multiple steps into a single hot-pressing phase.
- Structural Design of Fire-Retardant Boards: We produce fire-retardant engineered boards that can be used as a decorative surface while retaining safety standards, ensuring compliance with GB14101-1993.
By implementing these innovations, YK Door Industry Co., Ltd. not only improves production efficiency but also maintains our commitment to providing superior fire safety solutions.
Conclusion
Understanding the production process of fire door frames and leaves is vital for manufacturers aiming to provide safe, reliable products. At YK, we are dedicated to enhancing our processes and maintaining compliance with national standards to ensure our customers receive the highest quality fire doors available.
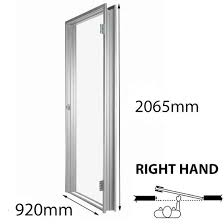