Do You Know How Wooden Fire Doors Are Manufactured?
- Current State of Flame-Retardant Wooden Materials and Products in China
- Challenges with Fire-Resistant Coatings
- Innovations in Flame-Retardant Treatment Technology
- Current Challenges in Fire-Rated Door Manufacturing
- Issues with Fire Retardant Coatings
- Innovations in Flame-Retardant Treatment
- Advanced Flame-Retardant Agents and Processing Techniques
- The Role of Fireproof Panels in Modern Construction
- Enhancing Fire Safety with Quality Wooden Fire Rated Doors
- Conclusion
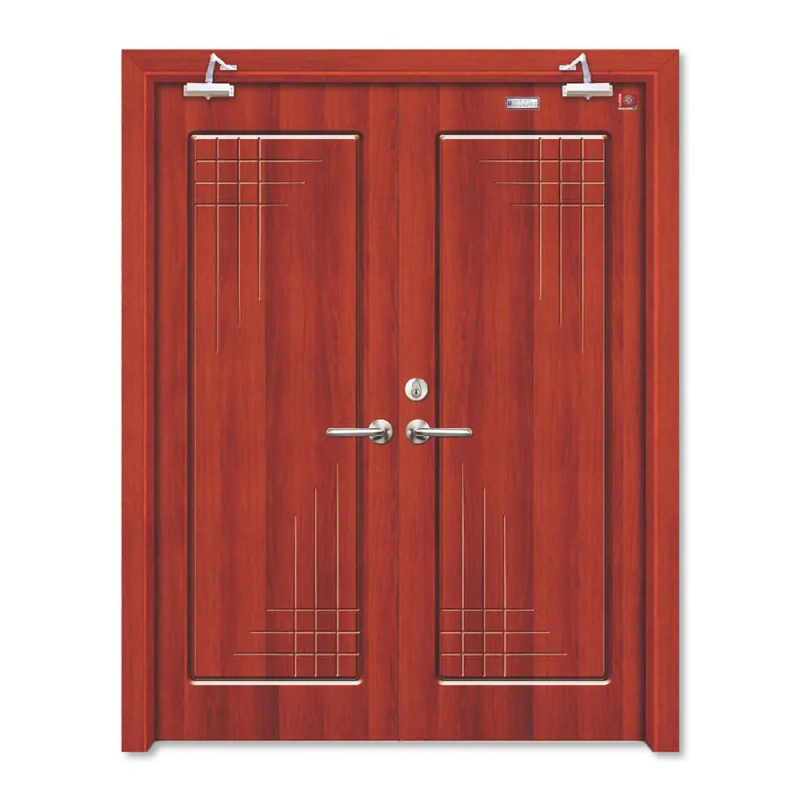
As a leading Chinese fire door manufacturer, we often get inquiries about the production process and technology behind wooden fire proof doors. In this SEO-optimized article, we will delve into the current state of flame-retardant wooden materials and products in China, the challenges faced by the industry, and the advanced techniques used to manufacture high-quality wooden fire rated doors. By understanding these aspects, you’ll gain insight into why choosing the right fire proof door is essential for safety and compliance.
Current State of Flame-Retardant Wooden Materials and Products in China
Over the past two decades, China has seen significant growth in the production of flame-retardant materials, particularly in the wooden fire door industry. Currently, there are 372 companies manufacturing wooden fire doors, 28 companies producing flame-retardant wood for interior decoration, and various enterprises involved in the production of flame-retardant plywood, decorative boards, and other materials. Despite these numbers, the adoption of flame-retardant wood and its products in building interiors remains limited, with most projects still relying on fire-resistant coatings for protection.
This reliance on fire-resistant coatings, rather than more advanced fire rated wooden doors or materials, reveals a considerable gap between China and developed countries in terms of fire safety standards. The main issues affecting the widespread use of flame-retardant wood and its products include:
- Product Variety and Quality: The current range and quality of products do not fully meet market demands, affecting their application in various construction projects.
- Limitations of Wood Structure: Due to the porous nature of wood, liquid flame retardants struggle to penetrate deeply, making effective treatment challenging for most types of wood.
- Extended Production Cycle: Flame-retardant treatment requires a secondary drying process, taking anywhere from 15 to 45 days, which prolongs the production cycle significantly.
- Complex Operations and Material Loss: The process of treating and drying veneers can result in significant material loss and operational complexity.
- Reduction in Strength: After treatment, the strength of wood and engineered wood products can decrease by 15-40%, limiting their practical use in certain applications.
- High Costs: Flame-retardant wood products are relatively expensive, further hindering their adoption in construction projects.
- Lack of Regulatory Enforcement: Despite the existence of fire safety regulations, effective implementation and enforcement remain inconsistent.
Challenges with Fire-Resistant Coating
While using fire-resistant coatings on wood products provides some level of fire protection, it comes with several drawbacks:
- Aesthetic Compromise: Coating wood with fire-resistant materials often results in the loss of its natural texture and decorative appeal. Although thin, transparent coatings can preserve some of the natural grain, the application of more than 500g/m² significantly reduces the wood’s visual quality.
- Durability Issues: Over time, coatings can crack, diminishing both fire protection and aesthetic appearance.
- Labor-Intensive Application: Applying fire-resistant coatings requires multiple layers—at least three coats are necessary—which increases the complexity and workload during construction.
- Environmental Concerns: Water-based coatings often have poor water and moisture resistance, while solvent-based coatings pose environmental hazards. Currently, no fire-resistant coatings on the market have a lifespan exceeding three years.
Innovations in Flame-Retardant Treatment Technology-How Wooden Fire Doors Are Manufactured?
To address these challenges, both domestic and international researchers have developed new methods for improving the flame-retardant properties of wood and engineered wood products. These methods aim to enhance the penetration and uniform distribution of flame retardants within the wood, ensuring that wooden fire proof doors meet the highest standards of safety and performance. How Wooden Fire Doors Are Manufactured.Some of these advanced techniques include:
- CO₂ Supercritical Fluid Treatment: This technique can treat almost all types of wood without significant adverse effects. Studies have shown that using a combination of CO₂ and formaldehyde can significantly increase the gas permeability of wood, depending on temperature and pressure variations.
- Laser Incision Technology: By creating micro-incisions on the wood surface without damaging its structure, laser technology allows for better penetration of flame retardants compared to traditional methods.
- Low-Pressure Steam Explosion: This method disrupts the closed vessel structures in the wood, improving permeability and facilitating better flame retardant distribution.
- Pre-Compression Treatment: By compressing wood laterally before treatment, the permeability of the material is improved, allowing for more efficient absorption of flame retardants.
- Microwave Heating: Pre-treating wood with microwave heating not only speeds up the heating process but also enhances the wood’s absorption of treatment chemicals.
- Vibration and Pressure Treatment: Applying vibrations during pressure treatment increases the absorption and retention of flame retardants in the wood.
- Use of Enzymes and Microorganisms: Research is being conducted on using biological agents to alter the permeability of wood, making it easier for flame retardants to penetrate deeply.
- Sonic and Ultrasonic Treatment: Utilizing sound waves during pressure treatment is another area being explored to improve wood’s permeability.
- Centrifugal Impregnation: This technique involves placing wood in a centrifuge to enhance the absorption of flame retardants under normal pressure conditions.
By employing these cutting-edge technologies, wooden fire rated doors can achieve a higher level of fire resistance and durability, making them an ideal choice for modern construction projects.
As a leading manufacturer of fireproof doors in China, Yunnan Guangdun Door Industry Co., Ltd. is dedicated to enhancing fire safety solutions through innovative technology and practices. This article explores the current challenges in the fire-rated door market and presents advanced techniques for improving product quality and efficiency, aiming to optimize our online presence on Google with relevant long-tail keywords such as fireproof door, fire rated door, wooden fireproof door, and others.
Current Challenges in Fire-Rated Door Manufacturing-How Wooden Fire Doors Are Manufactured.
- Limited Product Variety and Quality
The existing range of fire-rated doors does not fully meet market demand. This discrepancy necessitates the development of diverse products that can cater to various consumer needs. - Structural Limitations of Wood
Due to the porous nature of wood, liquids have difficulty penetrating the majority of wood types. As a result, most wood cannot undergo effective flame-retardant impregnation treatment, impacting the production of high-quality wooden fireproof doors. - Extended Production Cycles
Flame-retardant treatments require secondary drying, which can take anywhere from 15 to 45 days, thus prolonging the overall production time for fire-rated doors. - Handling Challenges During Treatment
The process of flame-retardant impregnation and drying can lead to significant damage to the veneer, complicating the operational process. - Strength Reduction Post-Treatment
The flame-retardant treatment can reduce the strength of both wood and engineered boards by 15% to 40%, affecting the overall application and effectiveness of fireproof doors. - High Treatment Costs
The cost of fire-retardant treatment for wood products tends to be high, which can deter consumers from investing in quality fire-rated doors. - Regulatory Compliance Issues
Effective implementation of fire safety regulations remains inadequate, leading to gaps in the quality assurance of fire-rated door products.
Issues with Fire Retardant Coatings
Utilizing fire retardant coatings for wood and its products poses several challenges:
- Loss of Aesthetic Appeal
While thin transparent fire retardant coatings can preserve the natural grain of the wood, applying more than 500 g/m² significantly diminishes the wood’s texture and appearance. - Durability of Coatings
Over time, coatings can crack, reducing both their fire protection and aesthetic qualities. - Increased Application Complexity
More than three applications of fire retardant coatings can complicate onsite installation and increase labor demands. - Environmental Concerns
Water-based fire retardant coatings lack sufficient waterproof and moisture-resistant properties, while solvent-based options contribute to environmental pollution. Currently, no fire retardant decorative coatings have a lifespan exceeding three years.
Innovations in Flame-Retardant Treatment
To address these challenges, several new technologies and methods for treating wood and engineered wood products have emerged:
- Supercritical CO2 Treatment
This method is effective for almost all wood species without adversely affecting the treated material. Research indicates that CO2 treatment can enhance gas permeability in wood samples, improving flame-retardant properties.How Wooden Fire Doors Are Manufactured. - Laser Scoring Techniques
Laser scoring does not damage the wood structure and significantly improves the infusion of flame retardants, enhancing treatment effectiveness. - Low-Pressure Steam Explosion
This technique improves permeability by selectively destroying closed pores in wood, thus facilitating better absorption of flame retardants.How Wooden Fire Doors Are Manufactured. - Compression Pre-Treatment
Applying lateral compression to wood improves permeability by selectively damaging pore membranes. - Thermal Water Treatment
For coniferous wood, thermal water treatment can remove blockages in pores, thus enhancing permeability. - Oscillation Pressure Treatment
Combining oscillation with pressure treatment has shown to significantly increase the absorption of flame retardants. - Utilization of Enzymes and Microorganisms
Research into using enzymes and microorganisms to enhance wood permeability offers promising avenues for flame-retardant treatments. - Ultrasound Processing
Incorporating ultrasound during treatment has emerged as a method to improve the penetration of flame retardants. - Centrifugal Processing Technology
Centrifugal methods enhance the absorption of flame retardants in wood, significantly improving treatment efficiency.
Advanced Flame-Retardant Agents and Processing Techniques
Innovations in flame retardants primarily focus on inorganic P-N systems to enhance effectiveness, reduce moisture absorption, and lower toxicity:
- Use of Suitable Additives
Combining non-water-soluble flame retardants with emulsifiers can create a more effective treatment solution. - Dual Diffusion Techniques
These methods create water-insoluble compounds within wood, enhancing flame resistance. - Resin-based Flame Retardants
These not only provide fire resistance but also improve the physical and mechanical properties of wood products. - Multi-functional Treatment Agents
Research into agents that offer flame retardancy, anti-corrosion, and pest resistance is ongoing.
The Role of Fireproof Panels in Modern Construction
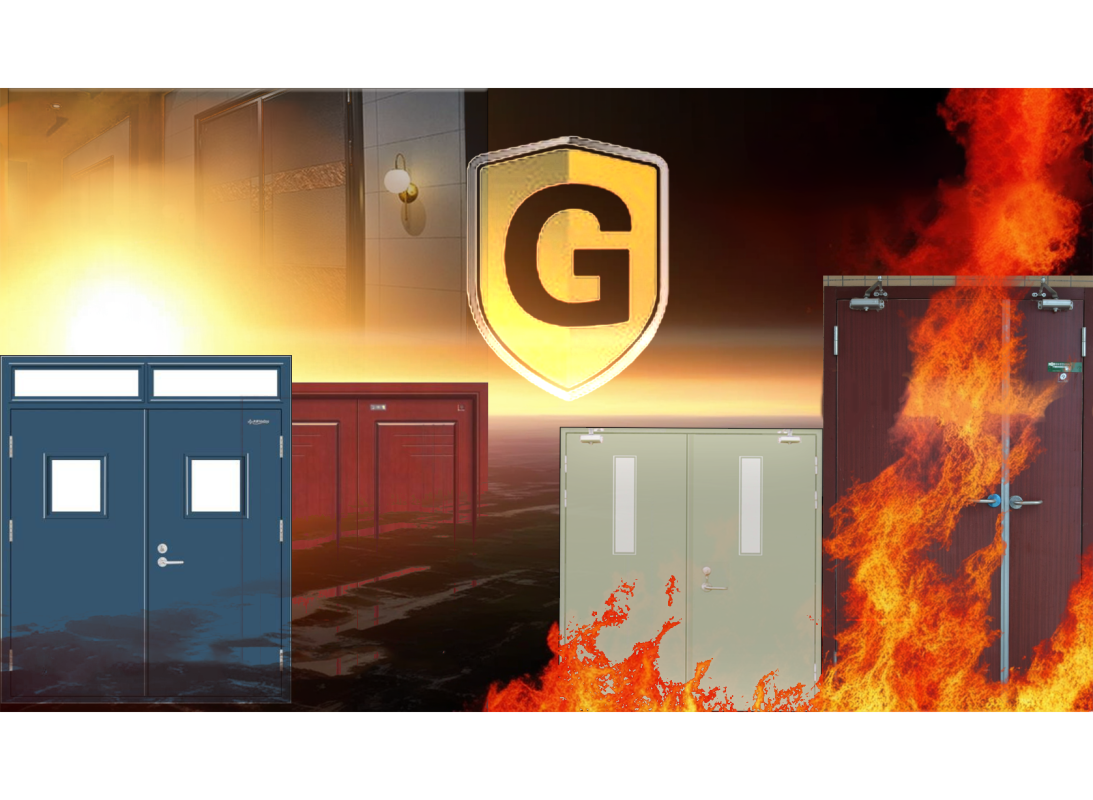
Fireproof panels, with thicknesses ranging from 0.2 to 5 mm, can significantly enhance the fire resistance of protected materials. In developed countries, these panels are widely used for fire protection in construction, overcoming the limitations of traditional fire retardant coatings and treatments.
Applications of Fireproof Panels:
- Protection and Decoration for Combustible Materials
Fireproof panels meet B1-level (flame-retardant) material requirements and enhance the aesthetic appeal of construction materials. - Replacing Traditional Coatings
These panels provide enhanced fire resistance for steel structures and combustible building materials, achieving fire resistance ratings of 1.0 to 3.0 hours. - Production of High-Quality Wooden Fire Doors
By increasing wood utilization and production efficiency, fireproof panels are essential in crafting superior wooden fireproof doors.
Enhancing Fire Safety with Quality Wooden Fire Rated Doors
At Yunnan Guangdun Door Industry Co., Ltd., we are dedicated to manufacturing top-quality wooden fire proof doors designed to withstand the most challenging fire safety standards. Our fire rated doors are meticulously crafted to ensure both safety and functionality, providing peace of mind for any building. In this article, we will explore critical aspects of wooden fire doors, including construction integrity, gap management, materials used, and essential fire door components that enhance their effectiveness.
1. The Importance of Gaps in Fire Rated Doors
During the manufacturing and installation of wooden fire proof doors, it is vital to consider potential gaps. These gaps can occur between the door leaf frame materials, between the frame and insulation materials, and between the door leaf and door frame. When subjected to testing in a furnace environment, these doors are exposed to positive pressure. If gaps exist from the fire-facing side to the rear, hot gases or flames can rapidly travel through, leading to the charring and burning of surrounding wood. Consequently, this can escalate the gap, eventually causing flames to appear on the rear surface of the fire door or igniting the insulating material.
To mitigate these risks, it is crucial to protect gaps to enhance the fire resistance performance of our wooden fire rated doors. For instance, regulations in Japan stipulate that high-temperature adhesive must be applied between the door frame materials and the filling materials, while expandable fireproof sealing strips should be used between the frame and the door leaf. In China, many manufacturers adopt similar practices but sometimes overlook these steps to save on production costs and maintain efficiency.
2. Structural Integrity of Fire Rated Doors
Unlike standard plywood doors, wooden fire proof doors require mortise and tenon joints to ensure structural stability. However, the complexity of this construction can lead to increased production challenges and material waste. As a result, some manufacturers resort to using dowel joints or staples common in regular plywood doors.
The insulation materials used within these doors typically consist of low-density products, such as aluminum silicate fibers or rock wool, which are inherently weak. To improve their stability, high-temperature adhesive and wire mesh are often necessary for reinforcement. Yet, the application of these materials can also slow production processes, prompting some manufacturers to skip these essential steps.
3. Types of Wooden Fire Rated Doors
Our wooden fire rated doors are categorized into eight different types based on their fire resistance ratings, ranging from easy to difficult classifications. When conducting sampling for type approval, the most challenging specifications are randomly selected from each fire resistance grade (A, B, C). Unfortunately, some manufacturers secure approvals for less challenging types but then indiscriminately expand their production range.
For glass-embedded fire doors, when the glass area exceeds a certain limit, additional testing of the rear surface temperature and heat radiation intensity is required. Some companies utilize smaller glass panels during certification to bypass these tests, compromising fire safety in actual production.
4. Essential Components of Fire Rated Doors
Critical components of fire rated doors include fireproof hinges, locks, closing devices, sequencers, and expandable fireproof sealing strips between door frames and leaves, as well as between double doors. All of these components must meet certification requirements. However, due to aesthetic and cost considerations, it is common to see ordinary hinges, locks, and closing devices used instead. The infrequent use of sequencers particularly undermines the fire and smoke containment capabilities of these doors.
5. Consistency Between Technical Documentation and Actual Samples
In accordance with the regulations governing fire door products, manufacturers must submit detailed structural diagrams (including elevation, section, and joint drawings) along with material lists to inspection centers for type approval. However, verifying some technical details, such as whether the wood has been treated with fire retardants, the content of these chemicals, or the species of wood used in the frames, can be challenging. These factors significantly influence the fire resistance of wooden fire doors, yet some manufacturers may fail to disclose this information or lower their product ratings to gain approval.
In practice, some manufacturers may reduce the content of fire retardants in wood or neglect to treat it altogether. Surveys of various companies indicate that a common practice is to simply soak the assembled door leaf and frame in a fire retardant solution for a few minutes. At room temperature and pressure, this method allows the solution to penetrate only about 2mm into the wood surface within an hour, proving ineffective for enhancing fire resistance.
6. Fire Retardant Treatment Processes
The quality of fire retardant treatment is crucial to the fire resistance limit of wooden fire doors. Many manufacturers treat this process as a critical control point in production. However, due to the lack of established procedures, each manufacturer may employ different and often suboptimal methods. Below are several recommended practices for effective fire retardant treatment:
- Moisture Content Control: The moisture content of the wood significantly affects its ability to absorb fire retardant solutions. Ideally, the moisture content should be below 15% for optimal absorption. Unfortunately, many manufacturers do not dry their wood before treatment, resulting in inconsistent quality.
- Proper Treatment Order: The treatment sequence should ideally be fire retardant solution first, followed by water, and then wood. This approach ensures that the wood absorbs the correct concentration of fire retardant from the start.
- Minimizing Solution Evaporation: Covering the treatment tank can help reduce evaporation of the fire retardant solution, ensuring a consistent concentration throughout the process.
- Cooling Before Removal: Allowing the treated wood to cool before removal can create a negative pressure that encourages further absorption of the fire retardant solution, enhancing overall quality.
Conclusion
By adhering to these best practices and prioritizing the integrity of our wooden fire rated doors, Yunnan Guangdun Door Industry Co., Ltd. aims to provide products that meet stringent fire safety standards. Investing in quality fire proof doors is not just a regulatory requirement but a vital step toward protecting lives and property. Our commitment to excellence in fire door manufacturing ensures that we remain a trusted name in fire safety solutions, helping you create safer environments for all.
For more information about our wooden fire rated doors and to explore our range of fire safety products, please visit our website or contact us today. Your safety is our priority!