Analysis of Fire Door Product Supervision and Quality Status
Yunnan Guangdun Door Industry Co., Ltd.
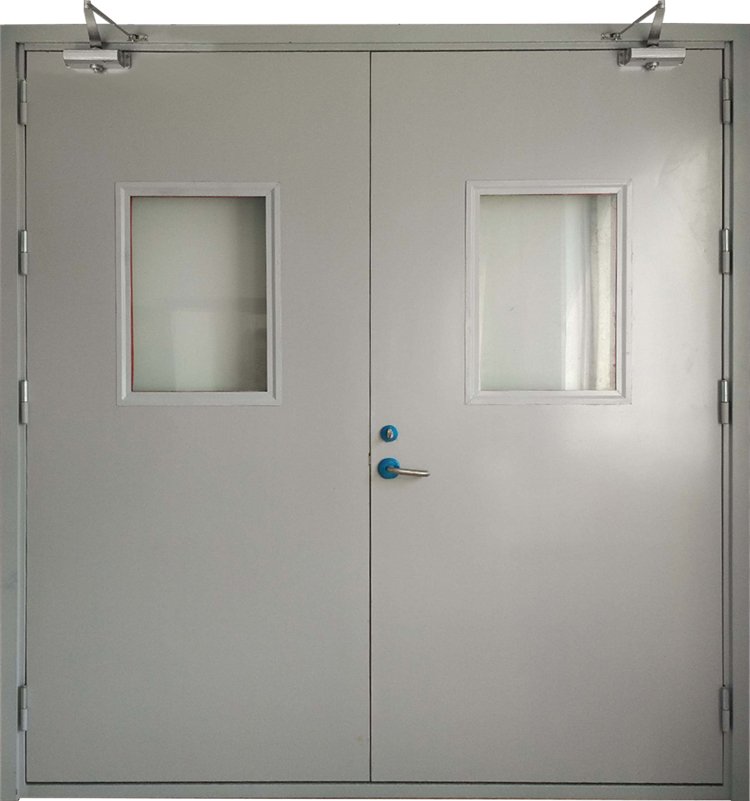
This paper outlines the current state of the fire door industry, focusing on market supervision and product standards. It provides a statistical analysis of the fire door quality inspections conducted over the past three years. The study investigates quality issues related to raw materials, production processes, and quality awareness. Recommendations for enhancing product quality are provided from three perspectives: strengthening raw material quality control, optimizing structural design, and improving the technical capabilities of enterprises.
Keywords: fire doors; fire resistance; quality analysis; fire-rated doors; fire door inspection.
Introduction
Fire doors play a critical role in protecting lives and property during a fire emergency. The market size of the fire door industry is closely linked to the real estate sector. With the ongoing downturn in the real estate market, the demand for fire doors has significantly decreased, intensifying market competition and leading to the closure of several small and micro-enterprises. However, with increasing societal awareness of fire safety and the continuous emergence of new materials and technologies, the range and application of fire doors are expanding, suggesting an overall upward trend for the industry.
Facing this era of both opportunities and challenges, most fire door manufacturers are shifting from a focus on rapid growth to pursuing high-quality development. It is crucial to enhance product performance, upgrade production lines, improve production processes, and strengthen quality management to seize developmental opportunities and gain a competitive edge in the market.
I. Market Regulation and Product Standards for Fire Doors
Fire doors are extensively used in various civil and commercial buildings such as office complexes, theaters, shopping malls, and sports facilities. Their ability to insulate against heat, withstand high temperatures, and provide excellent smoke control is their hallmark feature. Additionally, fire doors have the capability to automatically close during a fire, thereby compartmentalizing the affected area and minimizing the spread of fire and smoke.
Structurally similar to standard doors, fire doors include fire-resistant materials in the door frame, door leaf, and hardware components. Based on their fire resistance levels, fire doors are classified into three categories: A, B, and C, corresponding to fully insulated fire doors, partially insulated fire doors, and non-insulated fire doors, respectively. Class A fire doors, for example, are further divided into A1.50, A1.00, and A0.50 based on their fire resistance time.
China’s regulatory framework for fire door quality has evolved over time. The current national standard for fire doors has played a significant role in regulating the design, production, inspection, and supervision of fire door products. However, with advancements in materials, technologies, and fire safety requirements, some technical specifications in the 2008 standard have become outdated. A new national standard for fire doors is currently under review, expected to be released later this year. Key changes include stricter performance requirements, reduced mandatory use of specific materials, and new criteria for smoke leakage, water spray resistance, and signal reception for evacuation route fire doors. Additional requirements for core material specifications and mandatory maintenance checks are also included.
II. Fire Door Supervision and Inspection Status
A. National Supervision and Inspection
In 2021, the State Administration for Market Regulation conducted a national supervision and inspection of indoor building materials, covering fire door products from 198 companies in 18 provinces. The inspection revealed that 38 batches out of 198 were non-compliant, resulting in a failure rate of 19.2%. In 2022, the inspection scope expanded to include 138 batches from 138 companies across 21 provinces, focusing on key industrial clusters such as Hebei, Shandong, Zhejiang, Jiangsu, and Guangdong. This round of inspections found 19 non-compliant batches, with a reduced failure rate of 13.8%. In 2023, inspections in 18 provinces, including Zhejiang, Guangdong, Shandong, and Fujian, revealed 13 non-compliant batches out of 101, with a further reduced failure rate of 12.9%.
The gradual decline in the failure rate from 2021 to 2023 indicates improved adherence to fire resistance standards. Non-compliant products predominantly failed to meet the required fire resistance performance, underscoring the need for continued focus on improving material quality and production processes.
Recommendations for Quality Improvement
- Enhance Raw Material Quality Control: Implementing stringent quality checks for raw materials is crucial to ensure that all components used in the production of fire doors meet the highest standards of fire resistance and structural integrity.
- Optimize Structural Design: Rational design improvements can enhance the overall performance of fire doors, including their ability to withstand high temperatures and prevent the spread of smoke.
- Strengthen Technical Capabilities: Upgrading production equipment and adopting advanced manufacturing techniques can significantly improve the quality and consistency of fire door products, helping manufacturers to meet evolving regulatory requirements and market demands.
Analysis of Fire Door Product Supervision and Quality Status
Abstract: This article discusses the current situation in the fire door industry, covering market regulation and product standards. It provides an analysis of the supervision and inspection of fire door products over the past three years. The article identifies quality issues in raw materials, production processes, and quality awareness and offers effective recommendations for improving fire door quality through enhanced raw material control, rational structural design, and technological advancements.
1. Fire Door Market Regulation and Product Standards
Fire doors are widely used in various types of urban and rural buildings, such as office buildings, theaters, shopping malls, and sports venues. Their key features include heat insulation, fire resistance, and exceptional smoke prevention capabilities. In addition to these characteristics, fire doors are designed to self-close and self-latch, helping to contain the spread of fire and smoke, thereby minimizing damage and loss during a fire incident.
Structurally similar to ordinary doors, fire doors incorporate fire-resistant and insulating materials in the door frame, leaf, and associated hardware. Fire doors are classified into three categories based on their fire resistance rating: Class A, Class B, and Class C, corresponding to fully insulated fire doors, partially insulated fire doors, and non-insulated fire doors, respectively. Class A fire doors are further subdivided based on their fire resistance duration, such as A1.50, A1.00, and A0.50. Fire door configurations can include single-leaf, double-leaf, and multi-leaf designs, making them suitable for various applications, such as evacuation routes and equipment rooms. Fire doors are also categorized as normally open or normally closed. Normally open fire doors remain open under normal conditions and close automatically in case of fire, while normally closed fire doors stay shut and can be manually opened when needed, closing automatically afterward.
China has a long history of regulating fire door safety and quality. The current national standard for fire doors has significantly contributed to regulating the design, production, inspection, and supervision of fire door products. However, with the development of new materials and technologies, some critical technical requirements of the 2008 national standard have become outdated and no longer meet the needs of the fire door market and fire safety standards. A new standard for fire doors is currently under review and expected to be released this year. Major changes include stricter performance requirements, reduced mandatory material specifications, and new requirements for smoke-sealing performance, water spray resistance, and fire door linkage systems in evacuation routes. Additionally, the new standard introduces stringent requirements for core material properties, including burning performance, density, anti-halogen return, chloride ion leaching, and brominated flame retardant content. Other updates include the addition of fire door expiration dates on nameplates and mandatory periodic inspections, maintenance, and replacement by manufacturers and users.
2. Supervision and Inspection of Fire Doors
(1) Provincial Supervision and Inspection
From 2021 to 2023, a provincial market supervision bureau conducted a series of inspections on fire door manufacturers, covering 161 batches of samples from 120 local companies. The results showed 22 non-compliant batches, with an average non-compliance rate of 13.7%. The primary issue was inadequate fire resistance performance. The majority of the inspected samples were Class B fire doors, reflecting their prevalent use in building projects.
(2) Fire Resistance Performance of Fire Doors
One of the most critical quality indicators of a fire door is its fire resistance, which includes both integrity and insulation. Current standards define fire resistance integrity as the ability of a fire door to prevent flames and hot gases from penetrating its structure under standard heating conditions, or to maintain a non-combustible condition on the non-exposed side. Fire resistance insulation is defined as the ability of the non-exposed side to remain below a critical temperature for a specified duration under standard heating conditions.
To meet fire resistance integrity standards, a fire door must prevent ignition of the cotton pad, disallow penetration of the gap probe, and avoid sustained flaming on the non-exposed side for more than 10 seconds during the test. This performance relies on the rigidity and toughness of steel, the flame retardancy of wood, and the expansion characteristics of fire seals to prevent significant deformation and loss of fire containment.
For fire resistance insulation, the average temperature rise on the non-exposed surface should not exceed 140°C, with a maximum rise of 180°C on the door leaf and 360°C on the door frame. Failure to meet these standards can result in a reduced insulation duration. It is crucial to note that fire resistance integrity and insulation are interdependent; the integrity of the fire door ensures no flame or hot gas penetration, which in turn supports its insulation performance. In practice, failure to achieve integrity automatically results in non-compliance with insulation requirements. High-quality fire doors must meet both criteria as stipulated by national standards.
3. Recommendations for Improving Fire Door Quality
(1) Strengthening Raw Material Quality Control
The quality of raw materials significantly influences the fire resistance of fire doors. It is essential to use high-quality materials for the fire door core, door frame, and related components. Select materials with high thermal stability, strength, and low toxicity to improve fire door performance. For example, the use of high-density, fire-resistant core materials such as expanded perlite, magnesium oxide, and calcium silicate can enhance fire resistance. Similarly, choosing galvanized steel for door frames and ensuring compliance with thickness standards can improve durability and fire resistance.
(2) Rational Structural Design
Effective structural design is critical to the fire resistance of fire doors. Focus on strengthening weak points such as fire locks and frames, using fire-resistant boards and expansion seals at critical areas, and ensuring that all joints and seams are designed to withstand high temperatures. Implementing innovative designs, such as composite frames with heat-resistant features, can further enhance the overall performance of the fire door.
(3) Enhancing Technological Capabilities
Improving production technology is vital for meeting fire door standards. Manufacturers should invest in advanced production equipment and adopt modern manufacturing techniques to produce high-quality fire doors. Emphasize strict quality control at every stage of production and invest in R&D to stay ahead of industry trends, such as the development of multifunctional and smart fire doors. Comprehensive employee training on quality standards and production processes is also crucial for maintaining high product quality.
By addressing these key areas, fire door manufacturers can improve product quality and ensure compliance with evolving standards, ultimately contributing to enhanced fire safety in buildings.
Analysis of Fire Door Quality Issues and Improvement Strategies
1. Analysis of Fire Door Quality Issues
(1) Substandard Raw Materials
One of the most common issues encountered during fire resistance testing of fire doors is deformation and misalignment, especially where the gap between the door frame and door leaf is susceptible to high temperatures. Several factors contribute to this problem:
- Low-quality fire door core materials: Using inferior core boards, such as those prone to shrinkage or cracking under high temperatures, leads to loss of structural integrity and significantly diminishes the fire door’s ability to insulate against heat. Such core materials may also disintegrate or become pulverized, resulting in a failure to support the door structure during a fire.
- Inadequate steel thickness: If the steel sheets used in the fire door are too thin or lack rigidity, the door and frame can easily deform during fire testing. This can result in gaps that allow flames to escape, or even cause the door to collapse entirely.
- Poor-quality or improperly installed seals: Low-quality expansion seals or incorrect installation can lead to seal detachment when the door deforms under high temperatures, failing to effectively block the gaps. This can cause fire and smoke leakage, compromising the door’s performance in real fire scenarios.
(2) Incomplete Production Process
An improper fire door structure design can result in doors and frames deforming at different rates during exposure to high heat. This mismatch can lead to cracks and fire breaches, undermining the door’s integrity and accelerating the spread of fire. Common production issues include:
- Uneven core material distribution: Inadequate filling or poor compression of core materials, along with large seams in the fire door leaf, can result in insufficient protection of weak spots like fire locks and frames. This often leads to excessive heat transfer and shorter insulation times.
- Outdated equipment and manual processes: Many manufacturers use outdated machinery and low levels of automation. For example, manually cutting and inserting expanded perlite core materials can result in fractures or insufficient filling, leaving gaps that increase fire spread.
(3) Lack of Focus on Quality Control
The intense competition and pressure from high-quality foreign products have caused some manufacturers to prioritize profit over quality. Issues such as:
- Weak quality awareness: Some companies lack a robust quality management system and fail to implement standards effectively. This results in insufficient end-product inspections and discrepancies between production samples and tested samples.
- Non-compliance with production processes: Deviating from standard production processes—such as reducing the amount of core material or altering design specifications without proper testing—leads to non-compliant products that fail to meet safety standards.
2. Strategies for Improving Fire Door Quality
(1) Enhancing Raw Material Quality Control
The quality of fire door core materials and the primary structure materials are crucial to the overall performance of fire-rated doors. Common core materials like expanded perlite, magnesium oxide, foamed cement, vermiculite, and calcium silicate vary in their thermal insulation and mechanical properties. It’s essential to select materials with high thermal stability, strength, and low corrosiveness, and to optimize core material formulas or use new core materials to improve density and reduce moisture content.
- For steel materials, ensure that the thickness meets standards, and choose products from reputable manufacturers. Galvanized steel, known for its high corrosion resistance, is a good option.
- The performance of seals, glass, locks, hinges, and door closers also significantly impacts the quality of the fire door. Therefore, strict control over the selection and use of these components is necessary.
(2) Implementing Rational Structure Design
The design of the door leaf and frame structure plays a vital role in the effectiveness of a fire-resistant door. Key considerations include:
- Reinforcing weak points like fire locks and frames by connecting these components to the non-exposed side of the door leaf and placing fire-resistant boards or expansion seals at critical areas.
- Adopting composite door frame structures or heat-resistant designs, such as integrated door frames with heat-insulation grooves and sealing strips, to minimize thermal conduction. Ensuring that all connections and seams conform to relevant standards is crucial for maintaining the overall integrity of the fire door.
(3) Strengthening Technological Capabilities
The production technology of a fire door manufacturer directly affects whether the product meets national fire safety standards. To enhance quality:
- Update production equipment: Shift from producing low-end products to high-end ones by modernizing production facilities and adopting advanced technology.
- Implement strict quality controls: Enforce rigorous testing at every production stage, from raw material inspection to final product testing. Avoid practices such as using inferior materials or altering design specifications without proper validation.
- Invest in R&D: Stay ahead of the trends in fire door technology by investing in new materials and product innovations, such as eco-friendly, multifunctional, and smart fire door solutions.
- Comprehensive employee training: Regularly train employees in safety standards, production skills, and innovation to improve overall technical capabilities and foster a strong quality culture within the company.
By addressing these key areas, manufacturers can ensure that their fire doors meet the highest safety standards, helping to protect lives and property in the event of a fire.